Optimización del mantenimiento en la industria petrolera
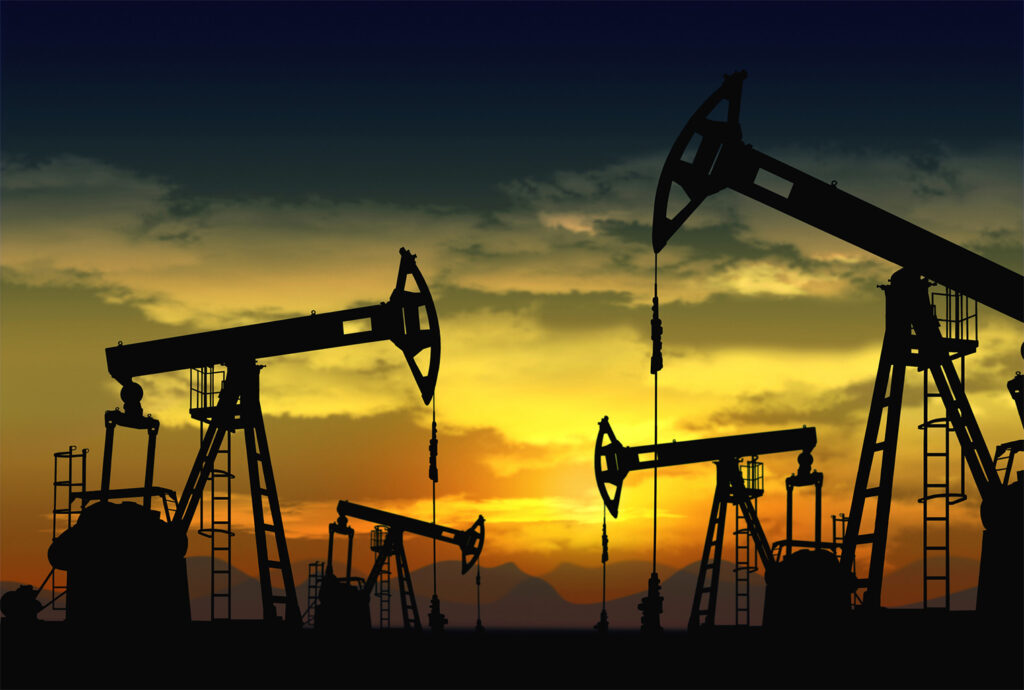
La industria petrolera es una de las más importantes a nivel mundial, ya que es responsable de la extracción, refinamiento y distribución de los combustibles fósiles que impulsan a la sociedad moderna. Sin embargo, el proceso de extracción y producción de petróleo implica una serie de riesgos y desafíos, entre ellos, el mantenimiento de los equipos y maquinarias utilizadas en esta industria.
Exploraremos la importancia de la optimización del mantenimiento en la industria petrolera. Analizaremos cómo una gestión eficiente del mantenimiento puede reducir los costos operativos, aumentar la vida útil de los equipos y minimizar los tiempos de inactividad. También discutiremos las tecnologías y estrategias que se están utilizando actualmente en la industria para mejorar el mantenimiento y maximizar la eficiencia en la producción de petróleo.
- Utilización de tecnología de monitoreo en tiempo real para detectar problemas antes de que se conviertan en fallas mayores
- Implementación de programas de mantenimiento preventivo para evitar problemas futuros
- Uso de análisis de datos para identificar patrones y tendencias en el desempeño de los equipos y programar mantenimientos de manera más eficiente
- Capacitación constante del personal de mantenimiento para que estén al tanto de las últimas técnicas y tecnologías
- Establecimiento de indicadores clave de desempeño para medir la eficacia del mantenimiento y poder hacer ajustes si es necesario
- Mantenimiento proactivo, anticipándose a los problemas y tomando medidas preventivas antes de que ocurran
- Implementación de un sistema de gestión de mantenimiento informatizado para facilitar el seguimiento y la programación de tareas
- Colaboración estrecha entre los departamentos de mantenimiento y producción para optimizar la planificación y minimizar el tiempo de inactividad
- Uso de tecnologías de control remoto para realizar labores de mantenimiento en áreas de difícil acceso o peligrosas para los trabajadores
- Implementación de un sistema de gestión de inventario eficiente para asegurar la disponibilidad de repuestos y minimizar el tiempo de espera en caso de reparaciones
- Preguntas frecuentes
Utilización de tecnología de monitoreo en tiempo real para detectar problemas antes de que se conviertan en fallas mayores
La utilización de tecnología de monitoreo en tiempo real es fundamental para optimizar el mantenimiento en la industria petrolera. Esta tecnología permite detectar problemas en los equipos y maquinarias antes de que se conviertan en fallas mayores, lo que a su vez reduce los costos y tiempos de reparación.
Mediante sensores y dispositivos de monitoreo, se recopila y analiza información en tiempo real sobre el estado y funcionamiento de los equipos. Esto proporciona datos clave sobre posibles problemas o desgastes que puedan afectar el rendimiento y la durabilidad de los activos.
Esta información se procesa de forma automática y se envía a los responsables de mantenimiento, quienes pueden tomar decisiones más rápidas y precisas en base a estos datos. Además, la tecnología de monitoreo en tiempo real permite establecer alarmas y notificaciones para advertir sobre condiciones anormales o inminentes fallas, lo que facilita la planificación de actividades de mantenimiento preventivo.
El uso de esta tecnología también permite implementar estrategias de mantenimiento predictivo, mediante la detección temprana de patrones o tendencias que indiquen un posible fallo en el futuro. Esto ayuda a evitar paradas no programadas de los equipos, minimizando así el impacto en la producción y reduciendo los costos asociados a reparaciones de emergencia.
La utilización de tecnología de monitoreo en tiempo real en la industria petrolera es esencial para optimizar el mantenimiento. Permite detectar problemas antes de que se conviertan en fallas mayores, reduciendo los costos y tiempos de reparación. Además, facilita la implementación de estrategias de mantenimiento preventivo y predictivo, mejorando la eficiencia operativa y prolongando la vida útil de los activos.
Implementación de programas de mantenimiento preventivo para evitar problemas futuros
En la industria petrolera, es de vital importancia implementar programas de mantenimiento preventivo con el objetivo de evitar problemas y fallos en los equipos y maquinarias utilizados en las operaciones diarias. Estos programas permiten mantener un control periódico y sistemático de las condiciones de los equipos, realizando inspecciones, ajustes y reparaciones necesarias para prevenir averías y prolongar la vida útil de los activos.
El mantenimiento preventivo se basa en la realización de actividades planificadas y programadas, que se llevan a cabo de manera regular para prevenir el deterioro y el desgaste prematuro de los equipos. Estas actividades incluyen inspecciones visuales, lubricación, limpieza, calibración y el reemplazo de piezas desgastadas o que se encuentren al final de su vida útil.
Ventajas del mantenimiento preventivo en la industria petrolera
- Reducción de costos: Al prevenir fallos y averías inesperadas, se evitan paradas no programadas de producción y se reducen los costos asociados a la reparación de equipos.
- Mejora de la seguridad: El mantenimiento preventivo garantiza el correcto funcionamiento de los equipos, minimizando el riesgo de accidentes y protegiendo la integridad de los trabajadores.
- Prolongación de la vida útil de los activos: Al cuidar y mantener adecuadamente los equipos, se logra prolongar su vida útil, lo que implica un mayor retorno de inversión para la empresa.
- Optimización de la producción: Al prevenir fallos y paradas no programadas, se garantiza la continuidad de la producción, evitando interrupciones y pérdidas de tiempo.
La implementación de programas de mantenimiento preventivo en la industria petrolera es fundamental para garantizar un funcionamiento eficiente y seguro de los equipos utilizados en las operaciones diarias. Esta estrategia permite reducir costos, mejorar la seguridad, prolongar la vida útil de los activos y optimizar la producción, brindando así ventajas competitivas a las empresas del sector.
Uso de análisis de datos para identificar patrones y tendencias en el desempeño de los equipos y programar mantenimientos de manera más eficiente
En la industria petrolera, el mantenimiento de los equipos es una tarea crucial para garantizar la eficiencia y seguridad en las operaciones. Sin embargo, realizar mantenimientos de manera periódica puede resultar costoso y generar tiempos de inactividad innecesarios.
Para optimizar el mantenimiento, es fundamental utilizar el análisis de datos para identificar patrones y tendencias en el desempeño de los equipos. De esta manera, es posible programar los mantenimientos de manera más eficiente, evitando intervenciones innecesarias y minimizando los tiempos de inactividad.
El análisis de datos permite obtener información valiosa sobre el estado de los equipos y su rendimiento. Mediante el monitoreo de variables como la temperatura, la presión y el consumo de energía, es posible identificar patrones que indiquen un deterioro progresivo en el desempeño de los equipos.
Además, el análisis de datos permite detectar tendencias a largo plazo, como el desgaste de piezas o la necesidad de ajustes y reemplazos. Con esta información, se pueden programar mantenimientos preventivos en momentos estratégicos, evitando así fallas catastróficas y reduciendo los costos asociados a reparaciones y reemplazos inesperados.
Para llevar a cabo el análisis de datos, es necesario contar con sistemas de monitoreo y registro de variables en tiempo real. Estos sistemas pueden incluir sensores y dispositivos conectados a los equipos, así como software de análisis y visualización de datos.
Una vez que se obtienen los datos, es posible utilizar técnicas estadísticas y algoritmos de aprendizaje automático para identificar patrones y tendencias. Estos análisis pueden realizarse de manera periódica, en tiempo real o de forma retrospectiva, dependiendo de las necesidades y recursos disponibles.
El uso del análisis de datos en la industria petrolera permite optimizar el mantenimiento de los equipos, programando intervenciones de manera más eficiente y evitando tiempos de inactividad innecesarios. Esto se traduce en una mejora en la eficiencia operativa, así como en la reducción de costos asociados a reparaciones y reemplazos imprevistos.
Capacitación constante del personal de mantenimiento para que estén al tanto de las últimas técnicas y tecnologías
Una de las estrategias clave para optimizar el mantenimiento en la industria petrolera es asegurarse de que el personal de mantenimiento esté constantemente capacitado y actualizado en las últimas técnicas y tecnologías. Esto es fundamental debido a la rápida evolución de la industria y a la introducción de nuevas metodologías y equipos.
Establecimiento de indicadores clave de desempeño para medir la eficacia del mantenimiento y poder hacer ajustes si es necesario
El establecimiento de indicadores clave de desempeño es fundamental para medir la eficacia del mantenimiento en la industria petrolera. Estos indicadores permiten evaluar y monitorear el rendimiento de los equipos y sistemas, así como identificar posibles áreas de mejora.
Existen diferentes tipos de indicadores que se pueden utilizar, dependiendo de los objetivos y metas específicas de cada empresa. Algunos ejemplos de indicadores clave de desempeño en el mantenimiento pueden incluir el tiempo medio entre fallas (MTBF), el tiempo medio de reparación (MTTR), el porcentaje de cumplimiento del plan de mantenimiento, entre otros.
Es importante que estos indicadores sean claros, medibles y relevantes para el negocio. Además, es necesario establecer metas específicas y realistas para cada indicador, de manera que se pueda medir el progreso y realizar ajustes si es necesario.
Para recopilar y analizar los datos necesarios para calcular los indicadores clave de desempeño, es recomendable utilizar sistemas de gestión de mantenimiento asistidos por computadora (CMMS). Estos sistemas permiten registrar y organizar la información sobre las actividades de mantenimiento, lo que facilita la generación de informes y análisis.
Una vez que se han establecido los indicadores clave de desempeño y se ha implementado un sistema de recopilación de datos, es importante realizar un seguimiento regular y sistemático de los indicadores. Esto permite identificar tendencias, detectar problemas y tomar acciones correctivas de manera oportuna.
Además, es recomendable realizar revisiones periódicas de los indicadores clave de desempeño, con el fin de evaluar su relevancia y ajustarlos si es necesario. Los indicadores deben ser flexibles y adaptarse a los cambios en el entorno de la industria petrolera, así como a los objetivos y estrategias de la empresa.
El establecimiento de indicadores clave de desempeño es fundamental para medir la eficacia del mantenimiento en la industria petrolera. Estos indicadores permiten evaluar el rendimiento de los equipos y sistemas, identificar áreas de mejora y realizar ajustes si es necesario. Para ello, es necesario utilizar sistemas de gestión de mantenimiento y realizar un seguimiento regular de los indicadores.
Mantenimiento proactivo, anticipándose a los problemas y tomando medidas preventivas antes de que ocurran
En la industria petrolera, el mantenimiento es una parte fundamental para garantizar el correcto funcionamiento de los equipos y maquinarias utilizadas en la extracción, refinación y distribución de petróleo y sus derivados. Un mantenimiento adecuado no solo contribuye a evitar fallos y accidentes, sino que también ayuda a optimizar la eficiencia operativa y reducir costos.
En este sentido, el enfoque proactivo en el mantenimiento es clave. En lugar de esperar a que ocurran problemas y reaccionar ante ellos, es mucho más efectivo anticiparse a los mismos y tomar medidas preventivas para evitar su aparición. Este enfoque se basa en la idea de que es más eficiente y económico prevenir los problemas que solucionarlos una vez que se presentan.
Para implementar un mantenimiento proactivo en la industria petrolera, es necesario llevar a cabo una serie de acciones y estrategias. A continuación, se presentan algunas de las más importantes:
1. Planificación y programación de actividades de mantenimiento
Es fundamental contar con un plan de mantenimiento que incluya la programación de actividades periódicas para la inspección, limpieza y lubricación de los equipos. Estas actividades deben llevarse a cabo de manera regular y sistemática, siguiendo un calendario establecido. De esta forma, se pueden detectar posibles problemas en etapas tempranas y tomar las medidas necesarias antes de que se conviertan en fallos mayores.
2. Uso de tecnologías de monitoreo y detección de fallos
La implementación de sistemas de monitoreo y detección de fallos permite tener un control constante sobre el estado de los equipos. Estas tecnologías permiten identificar posibles problemas y desviaciones en el funcionamiento de los mismos, lo que facilita la toma de decisiones anticipadas para prevenir fallos. Algunas de las tecnologías más utilizadas incluyen el monitoreo de vibraciones, termografía, análisis de aceite y ultrasonido.
3. Capacitación y formación del personal de mantenimiento
El personal encargado del mantenimiento debe contar con la formación y capacitación adecuada para llevar a cabo sus tareas de manera eficiente. Es importante que estén familiarizados con los equipos y maquinarias utilizados en la industria petrolera, así como con las técnicas y metodologías de mantenimiento proactivo. Además, deben estar al tanto de las novedades tecnológicas y las mejores prácticas en la industria.
4. Implementación de un sistema de gestión de mantenimiento
Contar con un sistema de gestión de mantenimiento (SGM) es fundamental para organizar y controlar todas las actividades relacionadas con el mantenimiento. Este sistema permite llevar un registro detallado de las tareas realizadas, los equipos inspeccionados y los resultados obtenidos. Además, facilita la programación de actividades y el seguimiento de los indicadores clave de desempeño (KPIs) para evaluar la eficiencia del mantenimiento.
La optimización del mantenimiento en la industria petrolera requiere de un enfoque proactivo, basado en la anticipación de problemas y la toma de medidas preventivas. Para lograrlo, es necesario contar con una planificación y programación adecuada de actividades, el uso de tecnologías de monitoreo, la capacitación del personal y la implementación de un sistema de gestión de mantenimiento.
Implementación de un sistema de gestión de mantenimiento informatizado para facilitar el seguimiento y la programación de tareas
La implementación de un sistema de gestión de mantenimiento informatizado en la industria petrolera es esencial para optimizar el mantenimiento de las instalaciones y equipos utilizados en la extracción y procesamiento de petróleo. Este sistema permite llevar un seguimiento detallado de las tareas de mantenimiento realizadas, así como programar de manera eficiente las labores a realizar en el futuro.
El sistema de gestión de mantenimiento informatizado se compone de una serie de módulos y funcionalidades que permiten registrar y organizar la información relacionada con el mantenimiento. Entre las principales características de este sistema se encuentran:
- Registro de actividades: Permite registrar todas las actividades realizadas en el mantenimiento de las instalaciones y equipos, incluyendo reparaciones, inspecciones y calibraciones. Esta información se encuentra disponible de forma centralizada y se puede acceder fácilmente para consultar el historial de mantenimiento de cada equipo.
- Programación de tareas: Facilita la programación de las tareas de mantenimiento a realizar en el futuro, teniendo en cuenta la frecuencia de ejecución de cada actividad. Esto permite planificar de manera eficiente el trabajo y evitar paradas no programadas debido a la falta de mantenimiento preventivo.
- Asignación de recursos: Permite asignar los recursos necesarios para llevar a cabo las tareas de mantenimiento, como personal, herramientas y repuestos. Esto garantiza que se cuente con todo lo necesario para realizar el trabajo de manera adecuada y en el tiempo previsto.
- Generación de reportes: Permite generar reportes personalizados sobre el estado de las tareas de mantenimiento, el cumplimiento de los plazos, el uso de los recursos y otros indicadores clave. Estos reportes son de gran utilidad para evaluar la eficiencia del mantenimiento y tomar decisiones informadas.
La implementación de un sistema de gestión de mantenimiento informatizado en la industria petrolera es fundamental para optimizar el mantenimiento de las instalaciones y equipos. Este sistema permite llevar un seguimiento detallado de las tareas realizadas, programar eficientemente las labores futuras, asignar los recursos necesarios y generar reportes para evaluar la eficiencia del mantenimiento. Con esta herramienta, las empresas petroleras pueden reducir los tiempos de parada no programada, maximizar la vida útil de los equipos y mejorar la seguridad en las operaciones.
Colaboración estrecha entre los departamentos de mantenimiento y producción para optimizar la planificación y minimizar el tiempo de inactividad
En la industria petrolera, el mantenimiento es una parte crucial para garantizar la eficiencia y la seguridad de las operaciones. Sin embargo, el tiempo de inactividad causado por el mantenimiento puede resultar costoso y afectar la productividad.
Una forma de optimizar el mantenimiento en la industria petrolera es fomentar una colaboración estrecha entre los departamentos de mantenimiento y producción. Trabajar en conjunto permite una mejor planificación y coordinación de las actividades de mantenimiento, lo que a su vez reduce el tiempo de inactividad.
Para lograr una colaboración efectiva, es importante establecer canales de comunicación claros y abiertos entre los equipos de mantenimiento y producción. Esto incluye la realización de reuniones regulares, donde ambas partes puedan discutir los planes de producción y las necesidades de mantenimiento.
Además, es esencial que los equipos de mantenimiento estén actualizados sobre las operaciones de producción. Esto les permitirá anticipar las necesidades de mantenimiento y programar las actividades de manera eficiente. Por otro lado, los equipos de producción deben estar informados sobre los trabajos de mantenimiento planificados, para que puedan ajustar sus planes en consecuencia.
Una estrategia efectiva para optimizar el mantenimiento es implementar un sistema de gestión de mantenimiento asistido por computadora (CMMS, por sus siglas en inglés). Este sistema permite a los equipos de mantenimiento llevar un registro de las tareas realizadas, programar actividades futuras y gestionar los recursos necesarios.
Además, el CMMS puede proporcionar informes y análisis de datos que ayudan a identificar áreas de mejora en las operaciones de mantenimiento. Esto permite a los equipos de mantenimiento tomar decisiones más informadas y optimizar su trabajo.
La optimización del mantenimiento en la industria petrolera requiere una estrecha colaboración entre los departamentos de mantenimiento y producción. Esta colaboración permite una mejor planificación y coordinación de las actividades de mantenimiento, lo que a su vez reduce el tiempo de inactividad y mejora la eficiencia en las operaciones petroleras.
Uso de tecnologías de control remoto para realizar labores de mantenimiento en áreas de difícil acceso o peligrosas para los trabajadores
En la industria petrolera, es común encontrar áreas de difícil acceso o peligrosas para los trabajadores, como plataformas marítimas o estructuras elevadas. Para realizar labores de mantenimiento en estos lugares, se han implementado tecnologías de control remoto que permiten llevar a cabo las tareas necesarias sin arriesgar la integridad física de los trabajadores.
Una de estas tecnologías es el uso de drones equipados con cámaras y herramientas especializadas. Estos drones pueden ser controlados de forma remota por un operador, quien puede visualizar en tiempo real las imágenes captadas por la cámara y realizar las acciones necesarias. Por ejemplo, si se detecta una fuga en una tubería, el operador puede enviar el drone para inspeccionar el área y tomar medidas correctivas.
Otra tecnología utilizada son los robots submarinos, también conocidos como ROVs (Remotely Operated Vehicles). Estos robots son utilizados para inspeccionar y realizar labores de mantenimiento en estructuras sumergidas, como plataformas petrolíferas o tuberías submarinas. Los ROVs están equipados con cámaras de alta definición, luces y brazos mecánicos que permiten realizar diversas tareas, como reparar una fuga o limpiar una superficie.
Además de los drones y los ROVs, también se emplean otros dispositivos controlados de forma remota, como robots terrestres o herramientas teleoperadas. Estos dispositivos son utilizados para labores de mantenimiento en áreas de difícil acceso, como tanques de almacenamiento o estructuras elevadas. De esta manera, se evita exponer a los trabajadores a situaciones peligrosas o incómodas.
El uso de tecnologías de control remoto en la industria petrolera ha permitido optimizar el mantenimiento en áreas de difícil acceso o peligrosas para los trabajadores. Los drones, los ROVs y otros dispositivos controlados de forma remota han demostrado ser herramientas eficientes y seguras para llevar a cabo labores de mantenimiento, evitando así riesgos innecesarios y mejorando la productividad en la industria.
Implementación de un sistema de gestión de inventario eficiente para asegurar la disponibilidad de repuestos y minimizar el tiempo de espera en caso de reparaciones
La implementación de un sistema de gestión de inventario eficiente es fundamental para garantizar la disponibilidad de repuestos en la industria petrolera. Esto permite minimizar el tiempo de espera en caso de reparaciones, optimizando así el mantenimiento de los equipos y reduciendo los costos asociados.
Para lograr una gestión de inventario eficiente, es necesario utilizar herramientas tecnológicas especializadas que permitan llevar un control preciso de los repuestos disponibles, los niveles de stock y los tiempos de entrega.
Una de las estrategias más efectivas es utilizar un sistema de código de barras para etiquetar los repuestos y registrarlos en una base de datos centralizada. Esto facilita la identificación y búsqueda de los repuestos necesarios, evitando la pérdida de tiempo en la localización de los mismos.
Además, es importante establecer un proceso de control de inventario que incluya la realización de inventarios periódicos para identificar los repuestos que se encuentran en mal estado o que están próximos a vencer. Esto permite tomar decisiones anticipadas y evitar paradas no programadas por falta de repuestos.
Asimismo, se recomienda establecer acuerdos con proveedores confiables y establecer contratos de suministro a largo plazo. Esto asegura la disponibilidad de los repuestos necesarios en tiempo y forma, evitando retrasos en las reparaciones y optimizando el tiempo de respuesta ante cualquier eventualidad.
La implementación de un sistema de gestión de inventario eficiente es fundamental para optimizar el mantenimiento en la industria petrolera. Esto asegura la disponibilidad de repuestos, minimiza el tiempo de espera en caso de reparaciones y reduce los costos asociados. Utilizar herramientas tecnológicas, establecer procesos de control de inventario y establecer acuerdos con proveedores confiables son algunas de las estrategias clave para lograr una gestión de inventario eficiente.
Preguntas frecuentes
¿Qué es la optimización del mantenimiento en la industria petrolera?
Es un proceso que busca mejorar la eficiencia y reducir los costos del mantenimiento en las instalaciones petroleras.
¿Cuáles son los beneficios de la optimización del mantenimiento en la industria petrolera?
Permite minimizar los tiempos de parada de las operaciones, aumentar la vida útil de los equipos y reducir los gastos en reparaciones.
¿Cómo se realiza la optimización del mantenimiento en la industria petrolera?
Se utiliza la tecnología de mantenimiento predictivo, se establecen planes de mantenimiento preventivo y se implementan estrategias de gestión del ciclo de vida de los equipos.
¿Cuál es el papel del análisis de datos en la optimización del mantenimiento en la industria petrolera?
El análisis de datos permite identificar patrones y tendencias en el comportamiento de los equipos, lo que ayuda a tomar decisiones informadas sobre el mantenimiento.
Deja una respuesta
Tal vez te puede interesar: