Guía de los KPI más utilizados en mantenimiento
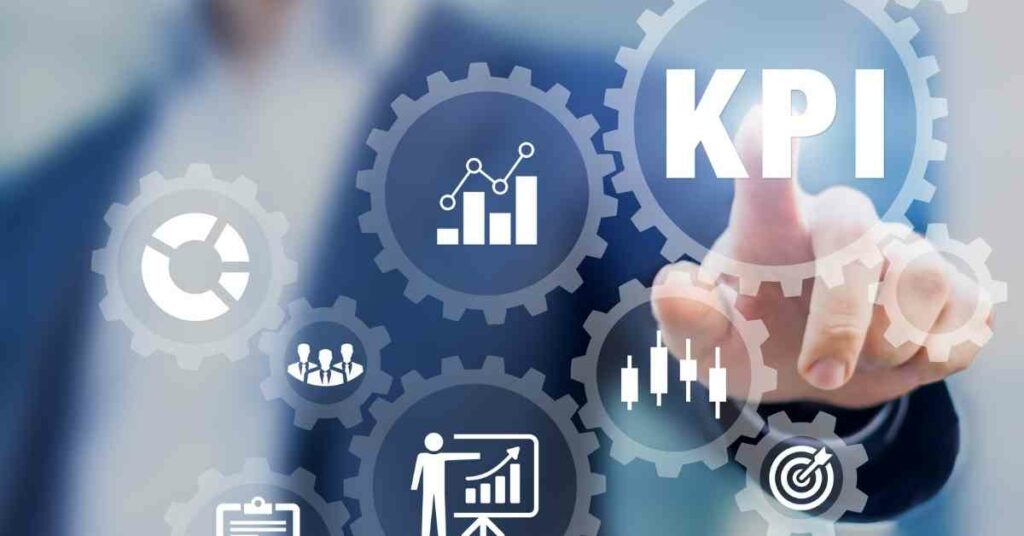
El mantenimiento es una actividad fundamental en cualquier organización que busca garantizar el correcto funcionamiento de sus activos y equipos. A través de la implementación de estrategias de mantenimiento, se busca minimizar los tiempos de parada, reducir los costos de reparación y aumentar la vida útil de los activos. Para lograr esto, es necesario medir y evaluar constantemente el desempeño del departamento de mantenimiento.
Exploraremos los KPI (Key Performance Indicators) más utilizados en el área de mantenimiento. Estos indicadores permiten medir y evaluar el desempeño de las actividades de mantenimiento, identificar áreas de mejora y tomar decisiones informadas para optimizar los recursos y maximizar la eficiencia del departamento de mantenimiento. Veremos los KPI más comunes, cómo se calculan y cómo se pueden utilizar para mejorar el rendimiento del mantenimiento en una organización.
- Los KPI (Key Performance Indicators) son métricas clave utilizadas para medir el desempeño en el mantenimiento
- Los KPI ayudan a evaluar la eficiencia, productividad y calidad del trabajo de mantenimiento
- Algunos de los KPI más utilizados en mantenimiento son el tiempo medio entre fallos (MTBF), el tiempo medio de reparación (MTTR) y la disponibilidad del equipo
- El MTBF mide el promedio de tiempo entre fallos de un equipo y permite evaluar su confiabilidad
- El MTTR mide el promedio de tiempo necesario para reparar un equipo averiado y ayuda a evaluar la eficiencia del equipo de mantenimiento
- La disponibilidad del equipo muestra el porcentaje de tiempo en que un equipo está en funcionamiento y disponible para su uso
- Otros KPI importantes en mantenimiento incluyen el índice de cumplimiento de planificación, el costo de mantenimiento por unidad de producción y el nivel de satisfacción del cliente interno o externo
- El índice de cumplimiento de planificación muestra qué tan bien se cumplen los planes de mantenimiento establecidos
- El costo de mantenimiento por unidad de producción evalúa la eficiencia del mantenimiento en términos de costos
- El nivel de satisfacción del cliente interno o externo mide la satisfacción de los usuarios finales con el trabajo de mantenimiento realizado
- Es importante seleccionar los KPI adecuados para cada organización, considerando sus objetivos y necesidades específicas
- Los KPI en mantenimiento deben ser medibles, relevantes, alcanzables y orientados a resultados
- Preguntas frecuentes
Los KPI (Key Performance Indicators) son métricas clave utilizadas para medir el desempeño en el mantenimiento
Los KPI (Key Performance Indicators) son métricas clave utilizadas para medir el desempeño en el mantenimiento. Estas métricas proporcionan información cuantitativa sobre el rendimiento de los procesos de mantenimiento y ayudan a evaluar la eficiencia y eficacia de las actividades de mantenimiento.
Los KPI ayudan a evaluar la eficiencia, productividad y calidad del trabajo de mantenimiento
Los Key Performance Indicators (KPI) son indicadores clave de rendimiento que permiten medir y evaluar el desempeño de un proceso o actividad. En el caso del mantenimiento, los KPI son herramientas fundamentales para evaluar la eficiencia, productividad y calidad del trabajo realizado.
Los KPI en el ámbito del mantenimiento nos proporcionan información valiosa sobre el rendimiento de los equipos, la disponibilidad de los recursos, la gestión de los tiempos y costos, entre otros aspectos. Estos indicadores nos permiten tomar decisiones informadas y mejorar continuamente nuestras prácticas de mantenimiento.
1. Porcentaje de tiempo de disponibilidad del equipo
Este KPI nos indica el porcentaje de tiempo en el que un equipo o maquinaria está disponible y en pleno funcionamiento. Para calcularlo, se divide el tiempo en el que el equipo está operativo entre el tiempo total analizado. Un alto porcentaje de disponibilidad indica una buena gestión del mantenimiento preventivo y correctivo.
2. Tiempo medio entre fallos (MTBF)
El MTBF es un indicador que mide el tiempo promedio que transcurre entre cada fallo de un equipo. Se calcula dividiendo el tiempo total de funcionamiento del equipo entre el número de fallos ocurridos en ese periodo. Un MTBF alto indica una mayor confiabilidad del equipo y una buena gestión de mantenimiento preventivo.
3. Tiempo medio de reparación (MTTR)
El MTTR es el tiempo promedio que se tarda en reparar un equipo o maquinaria después de un fallo. Se obtiene dividiendo el tiempo total de reparación entre el número de fallos ocurridos en un periodo determinado. Un MTTR bajo indica una rápida respuesta y solución a los problemas de mantenimiento.
4. Costo de mantenimiento por unidad de producción
Este KPI mide el costo promedio que se destina al mantenimiento de cada unidad de producción. Se calcula dividiendo el costo total de mantenimiento entre el número de unidades producidas en un periodo determinado. Permite evaluar la eficiencia y rentabilidad del mantenimiento en relación a la producción.
5. Porcentaje de cumplimiento de los planes de mantenimiento
Este indicador nos muestra el grado de cumplimiento de los planes de mantenimiento preventivo y predictivo establecidos. Se calcula dividiendo el número de actividades realizadas según el plan entre el número total de actividades programadas. Un alto porcentaje indica una buena planificación y ejecución de las tareas de mantenimiento.
Estos son solo algunos ejemplos de los KPI más utilizados en el ámbito del mantenimiento. Cada empresa puede adaptar y personalizar los indicadores según sus necesidades y objetivos. Lo importante es utilizar los KPI de manera efectiva para medir, evaluar y mejorar el desempeño de las actividades de mantenimiento.
Algunos de los KPI más utilizados en mantenimiento son el tiempo medio entre fallos (MTBF), el tiempo medio de reparación (MTTR) y la disponibilidad del equipo
El tiempo medio entre fallos (MTBF) es un KPI que mide la duración promedio entre dos fallos consecutivos de un equipo o sistema. Este indicador nos permite conocer la fiabilidad de los equipos y realizar una gestión preventiva del mantenimiento, evitando así tiempos de inactividad innecesarios.
Por otro lado, el tiempo medio de reparación (MTTR) es un KPI que nos indica el tiempo promedio que se tarda en reparar un equipo o sistema después de que se haya producido una falla. Este indicador nos ayuda a evaluar la eficiencia del personal de mantenimiento y a identificar posibles mejoras en los procesos de reparación.
La disponibilidad del equipo es otro KPI fundamental en el mantenimiento. Este indicador nos muestra el porcentaje de tiempo en el que un equipo o sistema está disponible para su uso. Una alta disponibilidad implica una menor probabilidad de tiempos de inactividad y una mayor eficiencia en la producción.
Además de estos KPI, existen otros indicadores muy utilizados en el mantenimiento, como el coste del mantenimiento por unidad de producción, el porcentaje de fallos recurrentes y el porcentaje de mantenimiento planificado frente a no planificado. Estos indicadores nos permiten evaluar el rendimiento global del departamento de mantenimiento y tomar decisiones basadas en datos para mejorar la eficiencia y reducir costes.
El MTBF mide el promedio de tiempo entre fallos de un equipo y permite evaluar su confiabilidad
El MTBF (Mean Time Between Failures) es un indicador clave utilizado en el área de mantenimiento para medir la confiabilidad de un equipo. Se calcula dividiendo el tiempo total de operación del equipo entre el número de fallos que ha experimentado en ese período.
Este KPI es especialmente útil para evaluar el desempeño de equipos críticos en una planta o instalación. Un MTBF alto indica que el equipo tiene una buena confiabilidad y que se requieren menos intervenciones de mantenimiento, lo que se traduce en una mayor disponibilidad del equipo y una menor probabilidad de interrupciones en la producción.
Por otro lado, un MTBF bajo indica que el equipo tiene una baja confiabilidad y que se requieren intervenciones de mantenimiento más frecuentes. Esto puede ser indicativo de problemas de diseño, calidad o de un mantenimiento inadecuado.
Es importante tener en cuenta que el MTBF solo mide el tiempo promedio entre fallos, pero no tiene en cuenta la gravedad de los fallos o el tiempo de reparación. Por lo tanto, es necesario complementar este indicador con otros KPIs para evaluar de manera más completa la confiabilidad y desempeño del equipo.
El MTTR mide el promedio de tiempo necesario para reparar un equipo averiado y ayuda a evaluar la eficiencia del equipo de mantenimiento
El MTTR (Mean Time To Repair) es uno de los KPI más utilizados en el área de mantenimiento. Este indicador se encarga de medir el tiempo promedio necesario para reparar un equipo averiado y tiene como objetivo evaluar la eficiencia del equipo de mantenimiento.
Para calcular el MTTR, se deben seguir los siguientes pasos:
- Registrar el tiempo de inicio de la avería.
- Registrar el tiempo de finalización de la reparación.
- Restar el tiempo de inicio al tiempo de finalización para obtener el tiempo total de reparación.
Es importante mencionar que el MTTR no tiene en cuenta el tiempo de espera antes de la reparación, únicamente se enfoca en el tiempo empleado en la reparación en sí.
Un MTTR bajo indica que el equipo de mantenimiento es eficiente y puede resolver las averías de manera rápida, lo cual es favorable para minimizar los tiempos de parada y maximizar la disponibilidad del equipo. Por otro lado, un MTTR alto puede indicar problemas en el proceso de reparación, falta de capacitación del personal o problemas en la gestión de repuestos y materiales.
Es importante destacar que el MTTR debe ser utilizado en conjunto con otros indicadores, como el MTBF (Mean Time Between Failures), para obtener una visión más completa de la eficiencia del equipo de mantenimiento.
La disponibilidad del equipo muestra el porcentaje de tiempo en que un equipo está en funcionamiento y disponible para su uso
La disponibilidad del equipo es un KPI fundamental en la gestión del mantenimiento, ya que muestra el porcentaje de tiempo en que un equipo está en funcionamiento y disponible para su uso. Este indicador es especialmente relevante en industrias donde la maquinaria y los equipos son cruciales para la producción.
Para calcular la disponibilidad del equipo, se utiliza la siguiente fórmula:
Disponibilidad del equipo = (Tiempo de funcionamiento / Tiempo total) * 100
El tiempo de funcionamiento se refiere al período en el que el equipo está operativo y sin interrupciones, mientras que el tiempo total se refiere al tiempo total disponible en un período determinado.
Una alta disponibilidad del equipo indica que este se encuentra en buen estado de funcionamiento y listo para ser utilizado. Por el contrario, una baja disponibilidad puede indicar problemas de mantenimiento o problemas recurrentes que afectan la operatividad del equipo.
Factores que pueden afectar la disponibilidad del equipo
Existen varios factores que pueden influir en la disponibilidad del equipo, entre ellos:
- Mantenimiento preventivo inadecuado o insuficiente
- Fallas recurrentes en el equipo
- Tiempo de inactividad no planificado debido a averías o reparaciones
- Problemas de suministro de repuestos o materiales
- Falta de capacitación del personal de mantenimiento
Es importante monitorear y analizar la disponibilidad del equipo de manera constante para identificar posibles áreas de mejora y tomar acciones correctivas. Esto permitirá optimizar la gestión del mantenimiento y garantizar una mayor eficiencia en la operación de los equipos.
Otros KPI importantes en mantenimiento incluyen el índice de cumplimiento de planificación, el costo de mantenimiento por unidad de producción y el nivel de satisfacción del cliente interno o externo
En el área de mantenimiento, existen diversos indicadores clave de rendimiento (KPI, por sus siglas en inglés) que son ampliamente utilizados para evaluar y medir el desempeño de los procesos y actividades relacionadas con el mantenimiento de activos. Además de los KPIs mencionados anteriormente, hay otros que también son importantes y que pueden proporcionar una visión más completa del rendimiento del departamento de mantenimiento.
Índice de cumplimiento de planificación
Este indicador mide la eficiencia con la que se cumplen los planes de mantenimiento programados. Se calcula dividiendo el número de tareas de mantenimiento planificadas completadas a tiempo entre el número total de tareas planificadas y multiplicando el resultado por 100. Un alto índice de cumplimiento de planificación indica una buena gestión de los recursos y una adecuada planificación de las actividades de mantenimiento.
Costo de mantenimiento por unidad de producción
Este KPI mide el costo promedio de realizar el mantenimiento de un activo por unidad de producción. Se calcula dividiendo los costos totales de mantenimiento entre la producción total en un período determinado. Este indicador permite evaluar la eficiencia del departamento de mantenimiento en términos de costo y determinar si existen oportunidades de mejora para reducir los costos de mantenimiento por unidad de producción.
Nivel de satisfacción del cliente interno o externo
Este KPI mide el grado de satisfacción de los clientes internos o externos con respecto al servicio de mantenimiento proporcionado. Puede medirse a través de encuestas de satisfacción, evaluaciones periódicas o mediante la recopilación de comentarios y sugerencias de los clientes. Un alto nivel de satisfacción del cliente indica una buena calidad en el servicio de mantenimiento y contribuye a la mejora continua de los procesos y actividades del departamento de mantenimiento.
El índice de cumplimiento de planificación muestra qué tan bien se cumplen los planes de mantenimiento establecidos
El índice de cumplimiento de planificación es un indicador clave que mide la eficiencia con la que se cumplen los planes de mantenimiento establecidos en una organización. Este KPI es fundamental para evaluar la efectividad de los procesos de planificación y programación en el departamento de mantenimiento.
Para calcular el índice de cumplimiento de planificación, se deben tener en cuenta dos variables: el número de órdenes de trabajo programadas y el número de órdenes de trabajo cumplidas en el período de tiempo establecido.
La fórmula para calcular este KPI es la siguiente:
Índice de Cumplimiento de Planificación = (Órdenes de trabajo cumplidas / Órdenes de trabajo programadas) x 100
Por ejemplo, si en un mes se programaron 100 órdenes de trabajo y se cumplieron 90, el índice de cumplimiento de planificación sería del 90%.
Un alto índice de cumplimiento de planificación indica que el departamento de mantenimiento está logrando ejecutar de manera efectiva las tareas programadas, lo que contribuye a la reducción de fallas y tiempos de inactividad no planificados. Por otro lado, un bajo índice de cumplimiento puede ser indicativo de problemas en la planificación o en la ejecución de las órdenes de trabajo.
Es importante monitorear regularmente el índice de cumplimiento de planificación y tomar las medidas necesarias para mejorarlo en caso de que sea necesario. Esto puede incluir la revisión y ajuste de los planes de mantenimiento, la capacitación del personal o la implementación de mejoras en los procesos de planificación y programación.
El índice de cumplimiento de planificación es un KPI esencial en el mantenimiento que permite evaluar la eficacia de los procesos de planificación y programación. Su seguimiento y mejora continua contribuyen a la optimización de los recursos y a la reducción de los tiempos de inactividad no planificados.
El costo de mantenimiento por unidad de producción evalúa la eficiencia del mantenimiento en términos de costos
El costo de mantenimiento por unidad de producción es uno de los indicadores clave de rendimiento (KPI, por sus siglas en inglés) más utilizados en la gestión de mantenimiento. Este KPI evalúa la eficiencia del mantenimiento en términos de los costos asociados a la producción de cada unidad.
Para calcular el costo de mantenimiento por unidad de producción, se deben sumar todos los costos relacionados con el mantenimiento, como el personal, los materiales, las herramientas y los equipos utilizados durante un periodo determinado. A continuación, se divide esta suma entre el número de unidades producidas durante el mismo periodo.
Este KPI es especialmente útil para evaluar la eficiencia del departamento de mantenimiento, ya que permite identificar si los costos asociados al mantenimiento son altos en relación con la producción. Si el costo de mantenimiento por unidad de producción es elevado, puede indicar que existen problemas en el proceso de mantenimiento que están afectando negativamente la eficiencia y aumentando los costos de producción.
Es importante tener en cuenta que este KPI no solo evalúa los costos directos del mantenimiento, sino también los costos indirectos, como el tiempo de inactividad de los equipos y las interrupciones en la producción. Incluir estos costos indirectos proporciona una visión más completa de la eficiencia del mantenimiento y su impacto en la productividad global de la empresa.
Para mejorar este KPI, es fundamental llevar a cabo un análisis detallado de los costos de mantenimiento y buscar oportunidades de optimización. Esto puede incluir la implementación de un plan de mantenimiento preventivo, la mejora de los procesos de reparación y reemplazo de equipos, y la capacitación del personal en buenas prácticas de mantenimiento.
El costo de mantenimiento por unidad de producción es un KPI fundamental para evaluar la eficiencia del mantenimiento en términos de costos. Este indicador permite identificar posibles problemas en el proceso de mantenimiento y buscar oportunidades de mejora para optimizar la eficiencia y reducir los costos de producción.
El nivel de satisfacción del cliente interno o externo mide la satisfacción de los usuarios finales con el trabajo de mantenimiento realizado
El nivel de satisfacción del cliente interno o externo es un indicador clave de rendimiento (KPI, por sus siglas en inglés) utilizado en el área de mantenimiento para medir la satisfacción de los usuarios finales con el trabajo realizado. Este KPI es fundamental para evaluar la calidad de los servicios de mantenimiento y garantizar la satisfacción de los clientes.
Para medir el nivel de satisfacción del cliente interno o externo, se pueden utilizar diferentes métodos y herramientas, como encuestas de satisfacción, entrevistas, análisis de quejas y reclamaciones, entre otros. Estos métodos permiten recopilar información relevante sobre las expectativas y opiniones de los usuarios finales, lo que a su vez ayuda a identificar áreas de mejora y tomar medidas correctivas.
Es importante destacar que la satisfacción del cliente interno o externo no solo se refiere a la calidad del trabajo de mantenimiento realizado, sino también a la capacidad de respuesta y comunicación del equipo de mantenimiento. Los usuarios finales valoran la rapidez y eficacia con la que se resuelven sus problemas o solicitudes de mantenimiento, así como la claridad y transparencia en la comunicación.
Medir y mejorar el nivel de satisfacción del cliente interno o externo es fundamental para garantizar la continuidad y el éxito de las operaciones de mantenimiento. Un cliente satisfecho es más propenso a seguir utilizando los servicios de mantenimiento y a recomendarlos a otros usuarios. Por lo tanto, es importante establecer objetivos claros en términos de satisfacción del cliente y realizar un seguimiento regular de los resultados para evaluar el desempeño y realizar mejoras continuas.
Es importante seleccionar los KPI adecuados para cada organización, considerando sus objetivos y necesidades específicas
Al momento de implementar un sistema de gestión de mantenimiento, es fundamental contar con indicadores clave de rendimiento (KPI, por sus siglas en inglés) que nos permitan evaluar de manera eficiente el desempeño de nuestras operaciones.
La selección de los KPI adecuados es crucial para medir y controlar los resultados de nuestros esfuerzos en mantenimiento. Cada organización tiene objetivos y necesidades específicas, por lo que es importante elegir los indicadores que sean relevantes y significativos para su contexto.
A continuación, presentamos algunos de los KPI más utilizados en mantenimiento:
- Tiempo medio entre fallas (MTBF): Este indicador mide el promedio de tiempo que transcurre entre una falla y otra en un equipo o sistema. Permite evaluar la confiabilidad de los activos y planificar las actividades de mantenimiento preventivo.
- Tiempo medio de reparación (MTTR): El MTTR indica el promedio de tiempo que se tarda en reparar una falla o avería. Este KPI es útil para evaluar la eficiencia de los procesos de reparación y determinar si se están cumpliendo los tiempos establecidos.
- Disponibilidad: La disponibilidad mide el porcentaje de tiempo en el que un equipo o sistema está operativo. Es un indicador clave para evaluar la capacidad de producción y determinar si los activos están disponibles cuando se necesitan.
- Costo de mantenimiento: Este KPI permite evaluar los costos asociados al mantenimiento de los activos. Incluye tanto los costos directos (mano de obra, repuestos, herramientas) como los indirectos (tiempo de inactividad, pérdida de producción).
- Índice de cumplimiento de mantenimiento: Este indicador evalúa en qué medida se están cumpliendo los planes de mantenimiento preventivo y predictivo. Permite identificar posibles desviaciones y tomar acciones correctivas oportunas.
Estos son solo algunos ejemplos de los KPI más utilizados en el ámbito del mantenimiento. Cada organización debe analizar su situación particular y definir los indicadores que mejor se adapten a sus necesidades y metas.
Es importante destacar que los KPI deben ser medibles, relevantes, alcanzables y estar alineados con los objetivos estratégicos de la organización. Además, es fundamental realizar un seguimiento constante de estos indicadores y utilizarlos como una herramienta para la toma de decisiones informada y la mejora continua.
Los KPI en mantenimiento deben ser medibles, relevantes, alcanzables y orientados a resultados
Los KPI (Key Performance Indicators) son indicadores clave de rendimiento que permiten medir el desempeño y la eficiencia de las actividades de mantenimiento en una organización. Estos indicadores son fundamentales para evaluar el cumplimiento de los objetivos establecidos y para tomar decisiones basadas en datos con el fin de mejorar continuamente los procesos de mantenimiento.
Seleccionar los KPI adecuados es crucial para garantizar que se estén midiendo los aspectos más relevantes y representativos del rendimiento en mantenimiento. Es importante tener en cuenta que los KPI deben ser medibles, relevantes, alcanzables y orientados a resultados.
Los KPI más utilizados en mantenimiento
A continuación, se presentan algunos de los KPI más utilizados en el ámbito del mantenimiento:
- Tiempo medio entre fallos (MTBF): Este indicador mide el tiempo promedio que transcurre entre dos fallos consecutivos en un equipo o sistema. Un MTBF alto indica una mayor confiabilidad y disponibilidad del equipo.
- Tiempo medio de reparación (MTTR): Este KPI mide el tiempo promedio que se tarda en reparar un equipo o sistema después de una falla. Un MTTR bajo indica una mayor eficiencia en la reparación y una menor pérdida de tiempo de producción.
- Porcentaje de tiempo de disponibilidad: Este indicador mide el porcentaje de tiempo en el que un equipo o sistema está disponible y listo para su uso. Un alto porcentaje de tiempo de disponibilidad indica una mayor eficiencia en el mantenimiento y una menor cantidad de tiempo de inactividad no planificado.
- Costo de mantenimiento: Este KPI mide el costo total de las actividades de mantenimiento en relación con el valor de los activos o equipos mantenidos. Un menor costo de mantenimiento indica una mayor eficiencia en la gestión de los recursos y una mejor optimización de los costos.
- Tasa de cumplimiento de los planes de mantenimiento: Este indicador mide el porcentaje de cumplimiento de los planes de mantenimiento programados. Un alto porcentaje de cumplimiento indica una mayor disciplina en la ejecución de las tareas de mantenimiento y una menor probabilidad de fallas no planificadas.
Estos son solo algunos ejemplos de los KPI más utilizados en el campo del mantenimiento. Es importante adaptar los indicadores a las necesidades y objetivos específicos de cada organización, teniendo en cuenta que los KPI deben ser claros, cuantificables y relevantes para poder tomar decisiones informadas y mejorar continuamente el desempeño en mantenimiento.
Preguntas frecuentes
1. ¿Qué son los KPI?
Los KPI (Key Performance Indicators) son indicadores clave de rendimiento que se utilizan para medir el desempeño de una actividad o proceso.
2. ¿Para qué se utilizan los KPI en mantenimiento?
Los KPI en mantenimiento se utilizan para medir la eficiencia, la productividad y la calidad del trabajo realizado, permitiendo tomar decisiones informadas para mejorar el rendimiento.
3. ¿Cuáles son los KPI más utilizados en mantenimiento?
Algunos de los KPI más utilizados en mantenimiento son el tiempo medio entre fallos (MTBF), el tiempo medio de reparación (MTTR), el porcentaje de cumplimiento de los planes de mantenimiento y el coste de mantenimiento por equipo.
4. ¿Cómo se calculan los KPI en mantenimiento?
Los KPI en mantenimiento se calculan utilizando fórmulas específicas para cada indicador. Por ejemplo, el MTBF se calcula dividiendo el tiempo total de operación entre el número de fallos ocurridos.
Deja una respuesta
Tal vez te puede interesar: