Diferencias entre controlador PID y controlador lógico programable
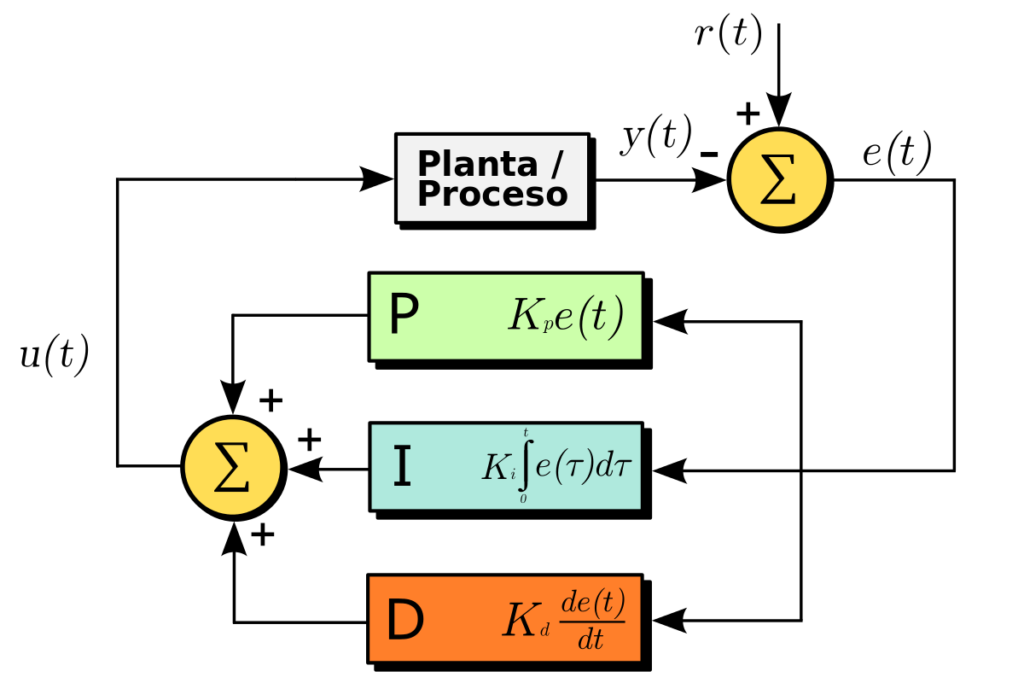
En el campo de la automatización industrial, existen diferentes tipos de controladores utilizados para regular y monitorear procesos. Dos de los más comunes son el controlador PID (Proporcional, Integral, Derivativo) y el controlador lógico programable (PLC, por sus siglas en inglés). Ambos desempeñan un papel importante en la optimización de los sistemas de control, pero tienen enfoques y características distintas.
Exploraremos las diferencias entre el controlador PID y el controlador lógico programable, destacando sus ventajas, desventajas y aplicaciones más comunes. Analizaremos cómo funcionan cada uno de ellos, sus componentes principales y cómo se utilizan en diferentes industrias. Además, examinaremos los criterios a considerar al elegir entre un controlador PID y un PLC, y qué factores pueden influir en la elección.
- El controlador PID es un algoritmo utilizado para regular un sistema en función de la diferencia entre la señal de entrada y la señal de referencia
- El controlador lógico programable (PLC, por sus siglas en inglés) es un dispositivo electrónico utilizado para controlar procesos industriales
- El controlador PID se basa en la retroalimentación y ajusta constantemente los parámetros para mantener el sistema en equilibrio
- El PLC utiliza una lógica programable para controlar las señales de entrada y salida y ejecutar tareas específicas
- El controlador PID es ampliamente utilizado en sistemas de control de temperatura, velocidad, presión, entre otros
- El PLC es utilizado en aplicaciones industriales donde se requiere control y automatización de procesos
- El controlador PID es más adecuado para sistemas que requieren un control más preciso y rápido
- El PLC es más adecuado para sistemas que requieren control de múltiples variables y tareas complejas
- El controlador PID se programa mediante el ajuste de los parámetros del algoritmo
- El controlador lógico programable se programa mediante la lógica de programación
- El PLC se programa utilizando lenguajes de programación específicos como ladder logic o estructurado text
- El controlador PID es más compacto y generalmente se encuentra en forma de módulo electrónico
- El controlador lógico programable es más versátil y flexible
- El PLC es más grande y se instala en armarios eléctricos o racks para su uso en sistemas industriales
- El controlador PID es más económico en comparación con un PLC
- El PLC es más costoso debido a su capacidad de control y flexibilidad
- El controlador PID es más comúnmente utilizado en aplicaciones de menor escala
- El controlador lógico programable es utilizado en aplicaciones de mayor escala
- El PLC es ampliamente utilizado en la industria para controlar procesos en tiempo real
- Preguntas frecuentes
El controlador PID es un algoritmo utilizado para regular un sistema en función de la diferencia entre la señal de entrada y la señal de referencia
El controlador PID (Proportional-Integral-Derivative) es un algoritmo utilizado comúnmente en la industria para regular y controlar sistemas automáticos. Se basa en la diferencia entre la señal de entrada y la señal de referencia para calcular y ajustar las acciones de control necesarias.
El controlador PID se compone de tres términos principales: proporcional, integral y derivativo. Cada uno de estos términos contribuye de manera diferente al cálculo de la salida del controlador.
El término proporcional se encarga de ajustar la salida del controlador en función de la diferencia proporcional entre la señal de entrada y la señal de referencia. Cuanto mayor sea esta diferencia, mayor será la contribución del término proporcional al cálculo de la salida del controlador.
El término integral tiene en cuenta la acumulación de errores pasados y busca reducir la diferencia acumulada entre la señal de entrada y la señal de referencia. Esto permite corregir errores persistentes y mejorar la estabilidad del sistema.
El término derivativo se encarga de anticiparse a los cambios en la señal de entrada y ajustar la salida del controlador en consecuencia. Esto ayuda a evitar oscilaciones y mejorar la respuesta del sistema ante cambios bruscos.
Por otro lado, los controladores lógicos programables (PLC por sus siglas en inglés) son dispositivos electrónicos programables utilizados para controlar y automatizar sistemas industriales. A diferencia del controlador PID, los PLC son más versátiles y pueden adaptarse a una amplia variedad de aplicaciones.
Los PLC son programados utilizando un lenguaje de programación específico, como ladder logic, que permite definir secuencias de eventos y acciones en función de entradas y salidas. Esto permite un control más flexible y sofisticado de los sistemas, ya que se pueden implementar algoritmos más complejos y lógicas más avanzadas.
Otra diferencia importante entre el controlador PID y los PLC es su enfoque. Mientras que el controlador PID se centra en el control de una variable específica, como la temperatura o la velocidad, los PLC pueden controlar múltiples variables y realizar diferentes tareas simultáneamente.
El controlador PID es un algoritmo utilizado para regular un sistema en función de la diferencia entre la señal de entrada y la señal de referencia. Por otro lado, los PLC son dispositivos programables más versátiles y flexibles que permiten controlar y automatizar sistemas industriales de manera más sofisticada y adaptada a diferentes aplicaciones.
El controlador lógico programable (PLC, por sus siglas en inglés) es un dispositivo electrónico utilizado para controlar procesos industriales
El controlador lógico programable (PLC, por sus siglas en inglés) es un dispositivo electrónico utilizado para controlar procesos industriales. Se trata de un sistema de control que se encarga de monitorear y regular el funcionamiento de maquinarias y procesos en diferentes industrias, como la automotriz, la alimentaria y la manufacturera.
El PLC se compone de una unidad central de procesamiento (CPU) que se encarga de ejecutar las instrucciones programadas, y de módulos de entrada y salida que permiten la comunicación con los sensores y actuadores del sistema. Además, cuenta con una memoria donde se almacenan los programas y datos necesarios para el control del proceso.
Funcionamiento del PLC
El funcionamiento del PLC se basa en la ejecución de un programa en lenguaje de programación de PLC, que suele ser un lenguaje gráfico similar a un diagrama de bloques. Este programa define las instrucciones que el PLC debe seguir para controlar el proceso de manera eficiente y segura.
El PLC recibe información de los sensores a través de los módulos de entrada, procesa esta información de acuerdo a las instrucciones programadas y envía señales a los actuadores a través de los módulos de salida. De esta forma, el PLC se encarga de regular el funcionamiento de los dispositivos conectados al sistema y de mantener el proceso dentro de los parámetros establecidos.
Una de las ventajas del PLC es su flexibilidad y capacidad de adaptación a diferentes procesos. Gracias a su programación, el PLC puede ser reconfigurado para adaptarse a cambios en el proceso o para controlar nuevas maquinarias. Además, permite la monitorización y registro de datos, lo que facilita el mantenimiento y la optimización del sistema.
Comparación con el controlador PID
A diferencia del PLC, el controlador PID (Proporcional, Integral, Derivativo) es un algoritmo de control que se utiliza para regular sistemas de control continuo. Este controlador se basa en el cálculo de tres componentes: la acción proporcional, la acción integral y la acción derivativa.
La acción proporcional se encarga de regular el sistema en función del error entre el valor deseado y el valor real. La acción integral, por su parte, corrige el error acumulado a lo largo del tiempo, mientras que la acción derivativa se encarga de predecir la tendencia futura del sistema y anticiparse a posibles errores.
En comparación con el PLC, el controlador PID es más adecuado para sistemas de control continuo, donde los cambios en el proceso son más suaves y graduales. Por otro lado, el PLC es más eficiente en sistemas de control discreto, donde los cambios en el proceso son más bruscos y rápidos.
El controlador lógico programable (PLC) es un dispositivo electrónico utilizado para controlar procesos industriales, mientras que el controlador PID es un algoritmo de control utilizado en sistemas de control continuo. Ambos tienen sus aplicaciones específicas y son herramientas fundamentales en el control de procesos en distintas industrias.
El controlador PID se basa en la retroalimentación y ajusta constantemente los parámetros para mantener el sistema en equilibrio
El controlador PID, también conocido como controlador proporcional-integral-derivativo, es un dispositivo utilizado para controlar y regular el comportamiento de un sistema. Se basa en el principio de la retroalimentación y ajusta constantemente los parámetros del sistema para mantenerlo en equilibrio.
El controlador PID utiliza tres componentes principales: el término proporcional (P), el término integral (I) y el término derivativo (D). Cada uno de estos términos contribuye de manera diferente al control del sistema.
El término proporcional (P) ajusta la salida del controlador en función del error entre el valor deseado y el valor real del sistema. Es decir, cuanto mayor sea el error, mayor será la salida del controlador para corregirlo.
El término integral (I) tiene en cuenta la acumulación de errores a lo largo del tiempo. A medida que el error persiste, este término aumenta la salida del controlador para corregir el error acumulado.
El término derivativo (D) tiene en cuenta la tasa de cambio del error. Si el error está cambiando rápidamente, este término aumenta la salida del controlador para anticiparse a los cambios en el sistema.
El controlador PID es un dispositivo que utiliza retroalimentación y ajustes constantes para mantener un sistema en equilibrio. Utiliza términos proporcional, integral y derivativo para controlar el sistema de manera eficiente.
El PLC utiliza una lógica programable para controlar las señales de entrada y salida y ejecutar tareas específicas
El controlador lógico programable (PLC) es un dispositivo electrónico utilizado en la automatización industrial para controlar las señales de entrada y salida, así como para ejecutar tareas específicas de forma lógica y secuencial. A diferencia del controlador PID, que se basa en un algoritmo de control proporcional, integral y derivativo, el PLC utiliza una lógica programable para realizar sus funciones.
Una de las principales diferencias entre el controlador PID y el PLC radica en su enfoque de control. Mientras que el controlador PID se basa en cálculos matemáticos para ajustar la salida a partir de la diferencia entre la consigna y la variable controlada, el PLC utiliza una serie de instrucciones programadas para controlar las señales de entrada y salida y ejecutar las acciones deseadas.
El PLC se programa utilizando lenguajes de programación específicos, como el ladder diagram (LD), el function block diagram (FBD) o el structured text (ST). Estos lenguajes permiten definir la lógica y las acciones que el PLC debe realizar en función de las señales de entrada y las condiciones establecidas.
Por otro lado, el controlador PID se configura mediante la sintonización de sus parámetros, como la constante proporcional, la constante integral y la constante derivativa. Estos parámetros determinan la forma en que el controlador responde a las variaciones en la señal de entrada y ajusta la salida para alcanzar el valor de consigna.
Otra diferencia importante entre el controlador PID y el PLC es su capacidad de procesamiento. Mientras que el controlador PID se utiliza principalmente para controlar variables continuas, como la temperatura o la presión, el PLC puede controlar una amplia gama de señales de entrada y salida, incluyendo sensores y actuadores, así como comunicarse con otros dispositivos o sistemas a través de diferentes protocolos.
El controlador PID y el PLC son dos enfoques diferentes de control utilizados en la automatización industrial. Mientras que el controlador PID se basa en un algoritmo matemático para ajustar la salida en función de la diferencia entre la consigna y la variable controlada, el PLC utiliza una lógica programable para controlar las señales de entrada y salida y ejecutar tareas específicas. Ambos enfoques tienen sus propias ventajas y desventajas, y su elección depende de las necesidades y requerimientos específicos de cada aplicación.
El controlador PID es ampliamente utilizado en sistemas de control de temperatura, velocidad, presión, entre otros
El controlador PID (Proporcional, Integral, Derivativo) es un tipo de controlador utilizado en sistemas de control automático para mantener una variable controlada en un valor deseado. Este tipo de controlador es ampliamente utilizado en diferentes aplicaciones, como el control de temperatura en sistemas de climatización, el control de velocidad en motores eléctricos y el control de presión en sistemas hidráulicos, entre otros.
El controlador PID se basa en tres componentes principales: el término proporcional, el término integral y el término derivativo. El término proporcional ajusta la salida del controlador en proporción al error entre el valor deseado y el valor medido. El término integral calcula y acumula la integral del error a lo largo del tiempo para eliminar los errores constantes. El término derivativo calcula la derivada del error para predecir su comportamiento futuro y ajustar la salida en consecuencia.
Por otro lado, el controlador lógico programable (PLC, por sus siglas en inglés) es un dispositivo utilizado en la automatización industrial para controlar y monitorear diferentes procesos. El PLC se programa utilizando un lenguaje de programación específico y se utiliza para controlar motores, válvulas, sensores y otros dispositivos en un sistema automatizado.
A diferencia del controlador PID, el PLC es más versátil y flexible, ya que puede adaptarse a diferentes aplicaciones y procesos. El PLC permite la programación de secuencias lógicas, temporizadores, contadores y otras funciones avanzadas para controlar y monitorear diferentes variables y procesos en tiempo real.
El controlador PID es ideal para aplicaciones en las que se requiere un control preciso y continuo de una variable, como la temperatura, velocidad o presión. Por otro lado, el PLC es más adecuado para sistemas más complejos y variables, ya que permite la programación de secuencias lógicas y otras funciones avanzadas.
El PLC es utilizado en aplicaciones industriales donde se requiere control y automatización de procesos
El controlador lógico programable, también conocido como PLC por sus siglas en inglés, es un dispositivo electrónico utilizado en aplicaciones industriales donde se requiere control y automatización de procesos. A diferencia del controlador PID, el PLC ofrece una solución más versátil y flexible para el control de sistemas complejos.
Funcionamiento del controlador lógico programable
El PLC se compone de una unidad central de procesamiento, también conocida como CPU, y de módulos de entrada y salida. La CPU ejecuta un programa almacenado en su memoria, el cual ha sido previamente diseñado y programado por un ingeniero o técnico especializado.
El programa del PLC se desarrolla utilizando un lenguaje de programación específico, como ladder, diagrama de bloques funcionales, texto estructurado o incluso lenguajes de programación de alto nivel. Este programa define las acciones que el PLC debe realizar en función de las entradas que recibe y de las condiciones establecidas por el programador.
Aplicaciones del PLC
El PLC se utiliza en una amplia variedad de aplicaciones industriales, como el control de maquinarias, sistemas de control de calidad, automatización de líneas de producción, control de procesos químicos, control de robots industriales, entre otros. Su versatilidad y capacidad de adaptación lo convierten en una herramienta fundamental para la optimización y eficiencia de los procesos industriales.
Diferencias con el controlador PID
A diferencia del controlador PID, que se centra en el control de procesos mediante la manipulación de variables como el error, la integral del error y la derivada del error, el PLC ofrece una solución más completa y flexible.
El controlador PID se utiliza principalmente en aplicaciones donde se requiere un control preciso y rápido de variables como la temperatura, la presión, el flujo, entre otras. Sin embargo, su capacidad se limita a la manipulación de estas variables y no permite la automatización de procesos complejos.
Ventajas del PLC
Una de las principales ventajas del PLC es su capacidad de adaptación a diferentes tipos de procesos y su flexibilidad para realizar modificaciones y ajustes en el programa de control sin necesidad de reemplazar hardware adicional.
Además, el PLC ofrece una mayor capacidad de procesamiento y almacenamiento de datos en comparación con el controlador PID. Esto permite la implementación de algoritmos más complejos y la gestión de sistemas más grandes y complejos.
Otra ventaja del PLC es su capacidad de comunicación con otros dispositivos y sistemas, lo que permite la integración y el intercambio de información con otros elementos de la planta industrial.
El PLC es una herramienta esencial en la automatización y control de procesos industriales. A diferencia del controlador PID, el PLC ofrece una solución más versátil y flexible, permitiendo el control y la automatización de sistemas más complejos. Su capacidad de adaptación, su capacidad de procesamiento y almacenamiento de datos, y su capacidad de comunicación lo convierten en una opción ideal para la optimización y eficiencia de los procesos industriales.
El controlador PID es más adecuado para sistemas que requieren un control más preciso y rápido
El controlador PID (Proporcional-Integral-Derivativo) es una técnica de control utilizada en sistemas de control automático. Se compone de tres componentes principales: el término proporcional, el término integral y el término derivativo.
El término proporcional calcula la diferencia entre el valor real y el valor deseado y ajusta la salida proporcionalmente a esta diferencia. Esto significa que cuanto mayor sea la diferencia, mayor será la corrección aplicada.
El término integral tiene en cuenta la acumulación de errores a lo largo del tiempo. Calcula el área bajo la curva de error y ajusta la salida en función de esta área acumulada. Este componente ayuda a eliminar los errores acumulativos y a alcanzar un control más preciso a largo plazo.
El término derivativo analiza la velocidad de cambio del error. Calcula la razón de cambio del error y ajusta la salida en función de esta velocidad de cambio. Esto ayuda a predecir el comportamiento futuro del sistema y a reaccionar rápidamente a cambios bruscos.
Por otro lado, el controlador lógico programable (PLC) es un dispositivo electrónico utilizado para controlar y automatizar procesos industriales. Se programa mediante un lenguaje de programación específico y se utiliza para controlar secuencias de encendido y apagado de dispositivos, así como para realizar operaciones lógicas y matemáticas.
En comparación con el controlador PID, el PLC es más adecuado para sistemas que requieren un control más simple y secuencial. Es especialmente útil en sistemas donde se requiere una lógica más compleja, como en la automatización de líneas de producción.
El PLC permite la programación de secuencias de encendido y apagado de dispositivos, así como la implementación de operaciones lógicas y matemáticas. Esto lo hace ideal para controlar procesos secuenciales o realizar operaciones lógicas más complejas, como el control de una línea de montaje.
El controlador PID es más adecuado para sistemas que requieren un control más preciso y rápido, mientras que el PLC es más adecuado para sistemas que requieren un control más simple y secuencial, así como para la automatización de líneas de producción.
El PLC es más adecuado para sistemas que requieren control de múltiples variables y tareas complejas
El controlador lógico programable (PLC) es una tecnología ampliamente utilizada en la industria para controlar y automatizar sistemas y procesos. A diferencia del controlador PID (Proporcional Integral Derivativo), el PLC es más adecuado para sistemas que requieren control de múltiples variables y tareas complejas.
El controlador PID se utiliza principalmente para controlar una única variable en un sistema. Utiliza una combinación de tres componentes: proporcional, integral y derivativo, para ajustar continuamente la salida y mantener la variable controlada en un valor deseado. Es especialmente útil en sistemas donde se requiere un control preciso y rápido, como en el control de temperatura en hornos industriales o en el control de velocidad de motores.
Por otro lado, el PLC ofrece una mayor flexibilidad y capacidad de control en comparación con el controlador PID. Puede manejar múltiples variables y tareas simultáneamente, lo que lo hace ideal para sistemas más complejos que requieren control de procesos, como líneas de producción o plantas de fabricación.
El PLC se programa utilizando un lenguaje de programación específico, como ladder logic, que permite crear secuencias lógicas y realizar acciones en función de las entradas y salidas del sistema. Esto permite una programación más intuitiva y fácil de entender para los técnicos y operadores.
Además, el PLC proporciona una mayor capacidad de expansión y modularidad. Puede agregar módulos de E/S adicionales y ampliar la funcionalidad del sistema sin necesidad de reemplazar todo el controlador. Esto hace que el PLC sea más versátil y escalable en comparación con el controlador PID.
Mientras que el controlador PID es más adecuado para sistemas simples que requieren un control preciso de una única variable, el PLC es la elección preferida cuando se necesita controlar múltiples variables y realizar tareas complejas en un sistema automatizado.
El controlador PID se programa mediante el ajuste de los parámetros del algoritmo
El controlador PID, o controlador proporcional-integral-derivativo, es un dispositivo utilizado en sistemas de control automático para mantener una variable de proceso en un valor deseado. Este controlador se programa ajustando los parámetros del algoritmo, los cuales son el coeficiente proporcional (P), el coeficiente integral (I) y el coeficiente derivativo (D).
El coeficiente proporcional determina la respuesta del controlador ante el error actual, es decir, la diferencia entre el valor deseado y el valor medido de la variable de proceso. Un mayor valor de P resulta en una respuesta más rápida pero también puede generar oscilaciones. Por otro lado, un valor muy bajo puede provocar una respuesta lenta o incluso inestable.
El coeficiente integral tiene en cuenta el error acumulado a lo largo del tiempo y ajusta la respuesta del controlador en función de este error acumulado. Un mayor valor de I ayuda a eliminar el error en estado estacionario, pero también puede causar un tiempo de respuesta más lento y aumentar el riesgo de oscilaciones.
El coeficiente derivativo se utiliza para predecir la tendencia futura del error y ajustar la respuesta del controlador en consecuencia. Un mayor valor de D puede ayudar a mejorar la estabilidad y reducir el tiempo de respuesta, pero también puede amplificar el ruido y provocar una respuesta inestable si se configura de manera incorrecta.
El controlador lógico programable se programa mediante la lógica de programación
Continúa escribiendo el contenido solo para ese encabezado:
Por otro lado, el controlador lógico programable, o PLC por sus siglas en inglés, es un dispositivo utilizado para controlar diferentes procesos industriales. Este controlador se programa mediante la lógica de programación, utilizando lenguajes como ladder, diagrama de bloques funcionales o texto estructurado.
El PLC se compone de una unidad central de procesamiento, entradas y salidas digitales y analógicas, así como de una interfaz de programación. La programación consiste en establecer relaciones lógicas entre las entradas y las salidas, de manera que se pueda controlar y supervisar el proceso deseado.
El lenguaje ladder es uno de los más utilizados en la programación de PLCs. Este lenguaje se basa en el uso de contactos y bobinas, que representan las entradas y salidas respectivamente. Mediante la conexión de estos elementos a través de relés virtuales, se pueden establecer las condiciones y acciones necesarias para controlar el proceso.
Otro lenguaje comúnmente utilizado en la programación de PLCs es el diagrama de bloques funcionales. Este lenguaje se basa en la interconexión de bloques de funciones, que representan diferentes operaciones lógicas o matemáticas. Estos bloques se conectan entre sí para establecer las relaciones y acciones necesarias para controlar el proceso.
Por último, el lenguaje de texto estructurado se utiliza en la programación de PLCs para realizar tareas más complejas y avanzadas. Este lenguaje se asemeja a la programación en lenguajes de alto nivel y permite la realización de operaciones matemáticas, lógicas y de control más sofisticadas.
Mientras que el controlador PID se programa ajustando los parámetros del algoritmo, el controlador lógico programable se programa mediante la lógica de programación utilizando diferentes lenguajes. Ambos controladores son ampliamente utilizados en la industria para controlar y supervisar procesos, pero difieren en su enfoque y forma de programación.
El PLC se programa utilizando lenguajes de programación específicos como ladder logic o estructurado text
El controlador lógico programable (PLC) es un dispositivo electrónico utilizado en la automatización industrial para controlar y supervisar procesos. A diferencia del controlador PID (Proporcional, Integral y Derivativo), el PLC se programa utilizando lenguajes de programación específicos como ladder logic o estructurado text.
El controlador PID es más compacto y generalmente se encuentra en forma de módulo electrónico
El controlador PID es una herramienta muy utilizada en el campo de la automatización industrial. Es un dispositivo compacto y generalmente se encuentra en forma de módulo electrónico. Su función principal es controlar y regular un proceso en base a una señal de retroalimentación.
El controlador PID utiliza un algoritmo que combina tres componentes: proporcionalidad (P), integral (I) y derivativo (D). Estos componentes trabajan juntos para asegurar una respuesta rápida y estable del sistema.
El controlador PID se utiliza principalmente en aplicaciones donde la precisión y la estabilidad son fundamentales. Algunos ejemplos de estas aplicaciones son el control de temperatura en hornos industriales, el control de velocidad en motores eléctricos y el control de nivel en tanques de almacenamiento.
El controlador lógico programable es más versátil y flexible
Continúa escribiendo el contenido solo para ese encabezado:
El controlador lógico programable (PLC) es otro dispositivo ampliamente utilizado en la automatización industrial. A diferencia del controlador PID, el PLC es más versátil y flexible, permitiendo la programación de diferentes lógicas y secuencias de control.
El PLC se compone de una unidad central de procesamiento, una memoria programable y una serie de entradas y salidas (E/S) para interactuar con el proceso que se desea controlar. Estas E/S pueden ser digitales o analógicas, lo que le confiere al PLC una gran capacidad de adaptación a diferentes aplicaciones.
El PLC se programa utilizando un lenguaje de programación específico, como el lenguaje de programación en escalera (Ladder), el lenguaje de programación estructurado (ST) o el lenguaje de programación de bloques de función (FBD). Estos lenguajes permiten la creación de diferentes secuencias de control y la implementación de lógicas más complejas.
El PLC se utiliza en una amplia variedad de aplicaciones, desde el control de procesos industriales hasta la automatización de edificios. Su versatilidad y flexibilidad lo convierten en una herramienta muy valiosa para los ingenieros y programadores de automatización.
El PLC es más grande y se instala en armarios eléctricos o racks para su uso en sistemas industriales
El PLC (Controlador Lógico Programable) es un dispositivo electrónico utilizado para controlar y automatizar sistemas industriales. Es más grande y se instala en armarios eléctricos o racks, lo que le permite manejar grandes cantidades de entradas y salidas.
El PLC se programa utilizando lenguajes de programación específicos, como el ladder diagram (LD) o el structured text (ST). Estos lenguajes permiten crear programas que controlan el comportamiento del PLC y, por ende, del sistema industrial.
El PLC se utiliza en una amplia variedad de aplicaciones industriales, como la automatización de líneas de producción, el control de motores, la monitorización de variables de proceso, entre otras.
Una de las principales ventajas del PLC es su flexibilidad. Puede ser reprogramado para adaptarse a diferentes necesidades y cambios en el proceso industrial. Además, puede comunicarse con otros dispositivos, como sensores y actuadores, a través de diferentes protocolos de comunicación.
El PLC es un dispositivo versátil y robusto utilizado en sistemas industriales para controlar y automatizar procesos. Su capacidad de programación y comunicación lo convierten en una herramienta indispensable en la industria.
El controlador PID es más económico en comparación con un PLC
El controlador PID es una solución más económica en comparación con un controlador lógico programable (PLC). Esto se debe a que el controlador PID está diseñado específicamente para realizar funciones de control y regulación en procesos industriales, mientras que un PLC es un dispositivo mucho más complejo que puede realizar múltiples tareas y funciones.
El controlador PID se enfoca en el control de variables como la temperatura, presión, flujo, nivel, entre otras, utilizando algoritmos matemáticos que ajustan automáticamente la salida del controlador para mantener la variable controlada en un valor deseado. Por otro lado, un PLC es capaz de realizar una amplia gama de funciones, como la lógica de control, la adquisición de datos, la comunicación con otros dispositivos, la gestión de alarmas, entre otras.
Debido a su funcionalidad más específica, el controlador PID es una opción más económica para aplicaciones que solo requieren control y regulación de variables. Además, los controladores PID suelen ser más fáciles de programar y configurar, lo que también contribuye a su menor costo en comparación con un PLC.
En contraste, un PLC es más costoso debido a su mayor capacidad y flexibilidad. Además del control y regulación de variables, un PLC puede realizar tareas más complejas, como el monitoreo de múltiples variables en tiempo real, la realización de cálculos complejos, la gestión de eventos y alarmas, la comunicación con otros dispositivos y sistemas, entre otras funciones.
Aunque un PLC puede realizar todas estas funciones adicionales, también requiere una programación más compleja y una configuración más detallada. Esto implica un mayor tiempo y esfuerzo en la puesta en marcha y mantenimiento del sistema, lo que se traduce en un mayor costo tanto en términos de mano de obra como de hardware.
El controlador PID es una opción más económica y sencilla cuando se requiere únicamente control y regulación de variables en un proceso industrial. Por otro lado, un PLC es más versátil y flexible, pero también más costoso y complejo de programar y configurar. La elección entre un controlador PID y un PLC dependerá de las necesidades específicas de cada aplicación y del presupuesto disponible.
El PLC es más costoso debido a su capacidad de control y flexibilidad
El controlador lógico programable (PLC) es una tecnología ampliamente utilizada en la automatización industrial debido a su capacidad de control y flexibilidad. Sin embargo, es importante tener en cuenta que el PLC puede ser más costoso en comparación con el controlador proporcional-integral-derivativo (PID).
El PLC es un dispositivo electrónico programable que utiliza una memoria programable para almacenar instrucciones y ejecutar tareas de control. Ofrece la ventaja de poder realizar múltiples tareas complejas y diversas, lo que lo hace ideal para aplicaciones industriales de gran escala. Además, el PLC puede manejar una amplia variedad de entradas y salidas, lo que le permite controlar y monitorear diferentes procesos en tiempo real.
Por otro lado, el controlador PID es un sistema de control que utiliza algoritmos matemáticos para ajustar continuamente la salida de control en función de las desviaciones entre el valor deseado y el valor real del proceso. A diferencia del PLC, el controlador PID es más simple y económico, ya que se centra en el control de un solo proceso en lugar de realizar múltiples tareas.
En términos de costos, el PLC tiende a ser más caro debido a su capacidad de control y flexibilidad. El PLC requiere una mayor inversión inicial, ya que implica la adquisición del hardware, como el controlador y las entradas/salidas, además del software de programación. Además, la programación del PLC puede ser más compleja y requiere un conocimiento más especializado, lo que puede aumentar los costos en términos de recursos humanos.
Por otro lado, el controlador PID es más económico en términos de costos iniciales y de programación. Debido a su simpleza, el controlador PID requiere menos componentes y una programación más sencilla. Además, la mayoría de los controladores PID están disponibles en el mercado a un costo relativamente bajo.
La elección entre un PLC y un controlador PID dependerá de las necesidades específicas de cada aplicación. Si se requiere un control más complejo y flexible, el PLC puede ser la opción ideal, aunque con un mayor costo asociado. Por otro lado, si se necesita un control más simple y económico, el controlador PID puede ser la mejor alternativa.
El controlador PID es más comúnmente utilizado en aplicaciones de menor escala
El controlador PID (Proporcional, Integral y Derivativo) es un dispositivo utilizado para controlar procesos automáticos. Es ampliamente utilizado en aplicaciones de menor escala, como el control de temperatura en electrodomésticos, control de velocidad en motores, entre otros.
El controlador PID se basa en el cálculo de tres componentes principales: la acción proporcional, la acción integral y la acción derivativa. La acción proporcional es responsable de ajustar la salida del controlador en función del error actual, la acción integral ajusta la salida en función del error acumulado y la acción derivativa ajusta la salida en función de la velocidad de cambio del error.
El controlador PID es altamente configurable y puede adaptarse a diferentes tipos de procesos. Es capaz de proporcionar una respuesta rápida y precisa a los cambios en la entrada y mantener la salida en un valor deseado.
El controlador lógico programable es utilizado en aplicaciones de mayor escala
El controlador lógico programable (PLC, por sus siglas en inglés) es un dispositivo utilizado para controlar procesos más complejos. Se utiliza en aplicaciones de mayor escala, como la automatización industrial, control de líneas de producción, entre otros.
El PLC se basa en la programación de una serie de instrucciones lógicas para controlar el funcionamiento de un sistema. Estas instrucciones lógicas pueden incluir operaciones matemáticas, comparaciones, temporizadores, contadores, entre otras. El PLC permite la implementación de lógica compleja y secuencias de control sofisticadas.
El PLC es altamente confiable y robusto, diseñado para funcionar en entornos industriales adversos. Puede manejar grandes cantidades de entradas y salidas, así como comunicarse con otros dispositivos y sistemas.
En resumen:
- El controlador PID es más comúnmente utilizado en aplicaciones de menor escala, como el control de temperatura en electrodomésticos.
- El controlador lógico programable es utilizado en aplicaciones de mayor escala, como la automatización industrial.
- El controlador PID se basa en el cálculo de tres componentes principales: la acción proporcional, la acción integral y la acción derivativa.
- El PLC se basa en la programación de una serie de instrucciones lógicas para controlar el funcionamiento de un sistema.
- El controlador PID es altamente configurable y puede adaptarse a diferentes tipos de procesos.
- El PLC es altamente confiable y robusto, diseñado para funcionar en entornos industriales adversos.
Tanto el controlador PID como el controlador lógico programable son herramientas útiles en el control de procesos automáticos, pero se utilizan en diferentes escalas y aplicaciones.
El PLC es ampliamente utilizado en la industria para controlar procesos en tiempo real
El controlador lógico programable (PLC por sus siglas en inglés) es un dispositivo electrónico utilizado en la industria para controlar y automatizar procesos en tiempo real. A diferencia del controlador PID (Proportional-Integral-Derivative), que se utiliza principalmente en sistemas de control de lazo cerrado, el PLC es versátil y puede adaptarse a una amplia gama de aplicaciones.
Funcionamiento del controlador PID
El controlador PID utiliza un algoritmo que combina tres componentes: proporcional, integral y derivativo. El componente proporcional ajusta la salida del controlador en función del error entre el valor deseado y el valor real. El componente integral acumula los errores pasados y ajusta la salida para eliminar el error acumulado. El componente derivativo ajusta la salida en función de la tasa de cambio del error.
Funcionamiento del controlador lógico programable
El PLC, por otro lado, utiliza un programa lógico para controlar el proceso. Este programa consiste en una serie de instrucciones que se ejecutan secuencialmente. El PLC puede recibir señales de entrada de sensores y tomar decisiones en función de estas señales para controlar los actuadores.
El controlador lógico programable es altamente adaptable y flexible. Puede ser programado para realizar una amplia variedad de tareas y puede ser reprogramado fácilmente para adaptarse a diferentes requisitos. Además, el PLC puede comunicarse con otros dispositivos y sistemas a través de protocolos de comunicación estándar.
Diferencias clave entre el controlador PID y el controlador lógico programable
- El controlador PID es adecuado para sistemas de control de lazo cerrado, mientras que el PLC es más versátil y se puede adaptar a diferentes tipos de aplicaciones.
- El controlador PID utiliza un algoritmo matemático para ajustar la salida en función del error, mientras que el PLC utiliza un programa lógico para controlar el proceso.
- El controlador PID es más adecuado para aplicaciones que requieren un control preciso y continuo, mientras que el PLC es más adecuado para aplicaciones que requieren una lógica de control más compleja y una mayor flexibilidad.
- El controlador PID es ampliamente utilizado en sistemas de control de procesos industriales, como control de temperatura, nivel y presión. En cambio, el PLC se utiliza en una amplia gama de aplicaciones, desde maquinaria industrial hasta sistemas de automatización de edificios.
Tanto el controlador PID como el controlador lógico programable son herramientas importantes en el campo de la automatización industrial. Cada uno tiene sus fortalezas y debilidades y es importante seleccionar el controlador adecuado según los requisitos del sistema y las aplicaciones específicas.
Preguntas frecuentes
¿Qué es un controlador PID?
Un controlador PID es un dispositivo utilizado para controlar un proceso mediante la retroalimentación de la señal de error y ajustando de forma proporcional, integral y derivativa.
¿Qué es un controlador lógico programable?
Un controlador lógico programable, o PLC, es un dispositivo electrónico programable utilizado para automatizar procesos industriales mediante la lógica de relés y la ejecución de instrucciones secuenciales.
¿Cuál es la principal diferencia entre un controlador PID y un PLC?
La principal diferencia radica en su funcionamiento: el controlador PID se enfoca en el control de procesos, mientras que el PLC se utiliza para la automatización de sistemas industriales más complejos.
¿Cuándo se recomienda utilizar un controlador PID y cuándo un PLC?
El controlador PID es más adecuado cuando se necesita un control preciso y continuo de un proceso, mientras que el PLC es más apropiado para automatizar sistemas con múltiples entradas y salidas y secuencias lógicas complejas.
Deja una respuesta
Tal vez te puede interesar: