Optimización de recursos en la gestión del mantenimiento
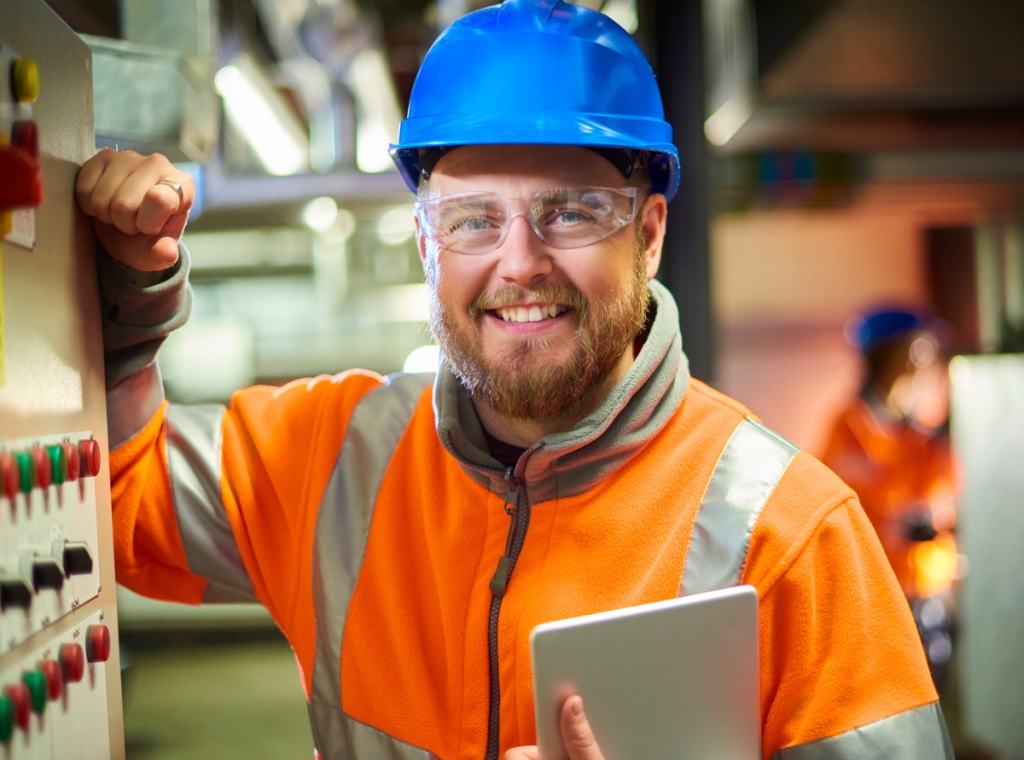
La gestión eficiente del mantenimiento es fundamental para asegurar el correcto funcionamiento de los equipos y maquinaria en cualquier empresa. Sin embargo, la falta de recursos y la falta de planificación adecuada pueden complicar esta tarea, generando costos innecesarios y tiempos de inactividad prolongados.
Exploraremos diferentes estrategias y técnicas para optimizar la gestión del mantenimiento, maximizando la utilización de los recursos disponibles y minimizando los tiempos de inactividad. Veremos cómo la implementación de un software de gestión del mantenimiento puede facilitar la planificación y programación de las tareas, así como el seguimiento de los trabajos realizados. También analizaremos la importancia de la formación y capacitación del personal, así como el uso de técnicas de mantenimiento predictivo para anticiparse a posibles fallos y evitar reparaciones costosas.
- Realizar un análisis de los recursos disponibles
- Establecer un plan de mantenimiento preventivo
- Utilizar software de gestión de mantenimiento
- Capacitar al personal en el uso eficiente de los recursos
- Implementar políticas de mantenimiento predictivo
- Priorizar las tareas de mantenimiento según su importancia
- Establecer indicadores de rendimiento para evaluar la eficiencia en la gestión
- Realizar seguimiento y control de los recursos utilizados
- Implementar medidas de ahorro energético en los equipos
- Integrar equipos y sistemas para optimizar la gestión del mantenimiento
- Mejorar la planificación y programación de las tareas de mantenimiento
- Realizar un mantenimiento correctivo eficiente para minimizar paradas no planificadas
- Realizar un análisis de costos para identificar oportunidades de ahorro
- Promover la cultura de la eficiencia en la gestión del mantenimiento
- Preguntas frecuentes
Realizar un análisis de los recursos disponibles
El primer paso para optimizar la gestión del mantenimiento es realizar un análisis exhaustivo de los recursos disponibles. Esto incluye tanto los recursos humanos como los recursos materiales.
En cuanto a los recursos humanos, es importante evaluar la cantidad de personal disponible y su nivel de experiencia y habilidades. También es necesario identificar las responsabilidades de cada miembro del equipo y asegurarse de que estén asignadas de manera eficiente.
En cuanto a los recursos materiales, es necesario evaluar el estado y la disponibilidad de los equipos y herramientas necesarios para llevar a cabo las tareas de mantenimiento. Esto incluye realizar un inventario de los equipos existentes, identificar cualquier equipo obsoleto o en mal estado, y asegurarse de que se mantengan las existencias adecuadas de repuestos.
Una vez que se haya realizado este análisis, se podrá tener una visión clara de los recursos disponibles y se podrán identificar posibles áreas de mejora. Por ejemplo, puede ser necesario contratar más personal, capacitar al personal existente en áreas específicas o invertir en nuevos equipos o herramientas.
Además, es importante establecer un sistema de seguimiento y control de los recursos, para asegurarse de que se están utilizando de manera eficiente y se están cumpliendo los plazos establecidos. Esto puede incluir la implementación de un software de gestión de mantenimiento que permita realizar un seguimiento en tiempo real de las tareas y los recursos utilizados.
Realizar un análisis de los recursos disponibles es fundamental para optimizar la gestión del mantenimiento. Esto permitirá identificar posibles áreas de mejora y tomar las medidas necesarias para asegurar que se están utilizando los recursos de manera eficiente.
Establecer un plan de mantenimiento preventivo
El primer paso para optimizar los recursos en la gestión del mantenimiento es establecer un plan de mantenimiento preventivo. Esta estrategia consiste en realizar inspecciones, revisiones y reparaciones periódicas en los equipos y maquinarias, con el objetivo de prevenir posibles fallas o averías.
Para implementar un plan de mantenimiento preventivo efectivo, es importante seguir algunos pasos clave:
- Identificar los equipos críticos: Es necesario identificar aquellos equipos y sistemas que son fundamentales para el funcionamiento de la organización. Estos son los que requieren un mayor nivel de atención y planificación en su mantenimiento.
- Establecer frecuencias de mantenimiento: Una vez identificados los equipos críticos, se deben establecer las frecuencias de mantenimiento adecuadas para cada uno. Esto puede variar según el tipo de equipo y su nivel de uso.
- Crear listas de verificación: Para asegurar que se realicen todas las tareas de mantenimiento necesarias, se deben crear listas de verificación detalladas. Estas listas deben incluir todas las inspecciones, revisiones y reparaciones que se deben realizar en cada equipo.
- Asignar responsabilidades: Es importante asignar responsabilidades claras a cada miembro del equipo de mantenimiento. Cada persona debe saber qué tareas le corresponden y cuándo deben ser realizadas.
- Registrar y analizar los datos: Durante el proceso de mantenimiento preventivo, es fundamental registrar y analizar los datos relevantes. Esto incluye información sobre las tareas realizadas, los tiempos de ejecución y cualquier incidencia o fallo detectado. Estos datos permitirán identificar patrones y tomar decisiones informadas para mejorar el plan de mantenimiento.
Implementar un plan de mantenimiento preventivo no solo ayuda a optimizar los recursos, sino que también reduce los tiempos de parada no planificados y aumenta la vida útil de los equipos. Además, contribuye a mejorar la seguridad y la fiabilidad de los mismos, lo que se traduce en una mayor eficiencia y rentabilidad para la organización.
Utilizar software de gestión de mantenimiento
La utilización de software de gestión de mantenimiento es una forma eficiente de optimizar los recursos en esta área. Estas herramientas permiten centralizar y organizar toda la información relacionada con el mantenimiento en un solo lugar, lo que facilita su seguimiento y control.
Además, este tipo de software ofrece funciones avanzadas que ayudan a mejorar la planificación y programación de las tareas de mantenimiento. Por ejemplo, es posible establecer calendarios de mantenimiento preventivo, asignar recursos de manera eficiente y realizar un seguimiento de los tiempos de ejecución de las tareas.
Asimismo, el software de gestión de mantenimiento permite llevar un registro detallado de los activos y equipos de la empresa, incluyendo su historial de mantenimiento y reparaciones realizadas. Esto facilita la toma de decisiones sobre la vida útil de los equipos y la planificación de inversiones en su reemplazo o actualización.
El uso de software de gestión de mantenimiento permite optimizar los recursos al mejorar la planificación y programación de las tareas, reducir los tiempos de inactividad de los equipos y optimizar la asignación de recursos humanos y materiales.
Capacitar al personal en el uso eficiente de los recursos
Uno de los aspectos clave para optimizar la gestión del mantenimiento es capacitar al personal en el uso eficiente de los recursos. Esto implica brindarles las herramientas y conocimientos necesarios para aprovechar al máximo los recursos disponibles y evitar su mal uso o desperdicio.
Para lograr esto, es importante llevar a cabo programas de capacitación que aborden temas como el manejo adecuado de las herramientas y equipos de trabajo, la correcta utilización de los materiales y suministros, y la implementación de prácticas de ahorro energético.
Además, es fundamental fomentar una cultura de responsabilidad y conciencia ambiental entre el personal. Esto implica promover buenas prácticas de uso de los recursos, como apagar las luces y los equipos cuando no se estén utilizando, evitar el derroche de materiales y adoptar medidas de reciclaje y reutilización.
Asimismo, es recomendable establecer indicadores de eficiencia en el uso de los recursos y realizar un seguimiento periódico de estos indicadores. Esto permitirá identificar posibles áreas de mejora y tomar medidas correctivas o preventivas para optimizar el uso de los recursos.
Capacitar al personal en el uso eficiente de los recursos es fundamental para optimizar la gestión del mantenimiento. Esto implica brindarles las herramientas y conocimientos necesarios, fomentar una cultura de responsabilidad y conciencia ambiental, establecer indicadores de eficiencia y realizar un seguimiento periódico de los mismos.
Implementar políticas de mantenimiento predictivo
El mantenimiento predictivo es una estrategia que consiste en monitorear constantemente el estado de los equipos y maquinarias, utilizando sensores y tecnología avanzada, con el objetivo de predecir posibles fallas y planificar las acciones de mantenimiento de manera anticipada.
La implementación de políticas de mantenimiento predictivo tiene como resultado una optimización de recursos considerable, ya que permite evitar paradas no planificadas de la producción y minimizar los costos asociados a reparaciones de emergencia.
Algunas de las ventajas de utilizar el mantenimiento predictivo son:
- Reducción de costos: Al anticiparse a posibles fallas, se pueden planificar las acciones de mantenimiento y adquirir los recursos necesarios de forma más eficiente, evitando gastos innecesarios.
- Aumento de la vida útil de los equipos: Al detectar y corregir problemas en etapas tempranas, se evita el desgaste y deterioro de los equipos, prolongando así su vida útil.
- Mejora en la disponibilidad de los equipos: Al evitar paradas no planificadas, se garantiza una mayor disponibilidad de los equipos para la producción.
- Optimización de los recursos humanos: Al contar con información precisa sobre el estado de los equipos, se pueden asignar las tareas de mantenimiento de manera más eficiente, optimizando el tiempo y esfuerzo del personal.
Priorizar las tareas de mantenimiento según su importancia
En la gestión del mantenimiento, es crucial priorizar las tareas según su importancia. Para lograr esto, es necesario evaluar la criticidad de cada tarea y asignarle una prioridad adecuada.
La importancia de una tarea de mantenimiento puede depender de varios factores, como el impacto que tendría su postergación en la operatividad del equipo o instalación, la seguridad de los trabajadores o la eficiencia del proceso. Es importante tener en cuenta estos aspectos al momento de establecer la prioridad.
Una forma común de priorizar las tareas es utilizando una escala de prioridades, donde se asigna un valor numérico a cada tarea. Por ejemplo:
- Urgente: Tareas que deben realizarse de inmediato para evitar daños mayores o riesgos para la seguridad.
- Importante: Tareas que deben realizarse en un plazo corto para garantizar la operatividad o eficiencia del equipo o instalación.
- Medio: Tareas que no son tan urgentes ni importantes, pero que deben realizarse dentro de un plazo razonable para evitar futuros problemas.
- Baja: Tareas de menor importancia que pueden postergarse sin causar mayores inconvenientes.
Al asignar una prioridad a cada tarea, es fundamental tener en cuenta los recursos disponibles, como el personal, el tiempo y los materiales necesarios. De esta forma, se puede optimizar la gestión del mantenimiento y asegurar que las tareas más críticas sean atendidas de manera prioritaria.
Establecer indicadores de rendimiento para evaluar la eficiencia en la gestión
En la gestión del mantenimiento es fundamental establecer indicadores de rendimiento que permitan evaluar la eficiencia de los recursos utilizados. Estos indicadores nos brindan información objetiva sobre el desempeño de los procesos y nos ayudan a identificar oportunidades de mejora.
Algunos de los indicadores más utilizados en la gestión del mantenimiento son:
- Tiempo medio entre fallos (MTBF): Este indicador nos permite medir la fiabilidad de los equipos y determinar cuánto tiempo transcurre en promedio entre cada fallo. Un MTBF alto indica que los equipos son más confiables y requieren menos intervenciones de mantenimiento.
- Tiempo medio de reparación (MTTR): Este indicador nos indica cuánto tiempo se tarda en promedio en reparar un equipo o sistema después de un fallo. Un MTTR bajo indica que el proceso de reparación es eficiente y se minimiza el tiempo de inactividad del equipo.
- Porcentaje de cumplimiento del plan de mantenimiento: Este indicador nos muestra qué tan cerca se cumple el plan de mantenimiento establecido. Un porcentaje alto indica que se están realizando todas las tareas de mantenimiento programadas y se están siguiendo los intervalos de tiempo establecidos.
- Costo de mantenimiento por unidad de producción: Este indicador nos permite evaluar la eficiencia económica de la gestión del mantenimiento. Nos indica cuánto se gasta en promedio en mantenimiento por cada unidad de producción generada. Un costo bajo indica que se están utilizando eficientemente los recursos disponibles.
Estos indicadores nos ayudan a identificar áreas de mejora en la gestión del mantenimiento y nos permiten tomar decisiones basadas en datos concretos. Además, nos permiten establecer metas y objetivos a alcanzar, y evaluar el impacto de las acciones implementadas.
Realizar seguimiento y control de los recursos utilizados
En la gestión del mantenimiento es importante realizar un seguimiento y control de los recursos utilizados. Esto nos permite optimizar su uso y lograr una mayor eficiencia en el proceso.
Para llevar a cabo este seguimiento, es necesario implementar un sistema de registro y control que nos permita conocer en todo momento qué recursos están siendo utilizados y en qué cantidad.
Una forma de hacer esto es mediante el uso de una lista de verificación, en la cual se detallen los recursos necesarios para cada tarea de mantenimiento. Esta lista puede incluir elementos como herramientas, materiales, equipos y personal necesario para llevar a cabo la tarea.
Es recomendable utilizar una combinación de listas desordenadas y listas ordenadas para organizar los recursos de manera clara y concisa. Por ejemplo, podemos utilizar una lista desordenada para enumerar los elementos necesarios y una lista ordenada para indicar la cantidad necesaria de cada elemento.
Además, es importante destacar aquellos recursos que son críticos o escasos, para poder gestionar su uso de forma más cuidadosa. Para esto, podemos utilizar la etiqueta <strong> para resaltar estos elementos en la lista.
Una vez que tenemos nuestra lista de recursos, es importante mantenerla actualizada y revisarla regularmente para asegurarnos de que estamos utilizando los recursos de manera eficiente. Esto nos permitirá identificar posibles problemas o áreas de mejora en la gestión de los recursos utilizados.
Realizar un seguimiento y control de los recursos utilizados en la gestión del mantenimiento nos permite optimizar su uso y lograr una mayor eficiencia en el proceso. Utilizar listas de verificación y resaltar los recursos críticos nos ayuda a organizar y gestionar los recursos de manera más efectiva.
Implementar medidas de ahorro energético en los equipos
Una de las estrategias clave para optimizar los recursos en la gestión del mantenimiento es implementar medidas de ahorro energético en los equipos utilizados. Esto no solo contribuye al cuidado del medio ambiente, sino que también permite reducir los costos asociados al consumo de energía.
Para lograr esto, es fundamental llevar a cabo un análisis exhaustivo de los equipos y sistemas utilizados en la empresa. Identificar aquellos que consumen mayor energía y evaluar las posibles soluciones para reducir este consumo.
Algunas medidas de ahorro energético que se pueden implementar son:
- Optimización de la carga y descarga de equipos: Es importante programar los equipos de manera eficiente, evitando tiempos de inactividad innecesarios y maximizando su rendimiento.
- Uso de tecnologías más eficientes: Reemplazar los equipos antiguos por aquellos que cuenten con tecnologías más eficientes en términos de consumo energético.
- Implementación de sistemas de apagado automático: Configurar los equipos para que se apaguen automáticamente cuando no estén en uso, evitando el consumo innecesario de energía.
- Control de la iluminación: Utilizar sistemas de iluminación inteligentes que se ajusten automáticamente a las necesidades de cada espacio, evitando el uso excesivo de luz artificial.
Estas medidas no solo contribuyen al ahorro energético, sino que también prolongan la vida útil de los equipos y reducen la necesidad de realizar mantenimientos correctivos, lo que a su vez disminuye los costos asociados a la gestión del mantenimiento.
Implementar medidas de ahorro energético en los equipos utilizados en la gestión del mantenimiento es una estrategia efectiva para optimizar los recursos y reducir costos. Además, contribuye al cuidado del medio ambiente y promueve la sostenibilidad en la empresa.
Integrar equipos y sistemas para optimizar la gestión del mantenimiento
La gestión eficiente del mantenimiento es fundamental para garantizar el correcto funcionamiento de los equipos y sistemas en cualquier organización. Sin embargo, a menudo nos encontramos con desafíos en cuanto a la optimización de los recursos y la coordinación de los diferentes equipos involucrados en esta tarea.
Una de las estrategias más efectivas para mejorar la eficiencia en la gestión del mantenimiento es la integración de equipos y sistemas. Esto implica establecer una comunicación fluida entre los distintos departamentos y utilizar herramientas tecnológicas que permitan un mejor seguimiento y control de las actividades de mantenimiento.
Beneficios de la integración de equipos y sistemas
1. Mejora de la planificación y programación: Al integrar los equipos de mantenimiento con los departamentos de producción y logística, es posible establecer una planificación más precisa y evitar interrupciones innecesarias en la producción. Además, se pueden programar las tareas de mantenimiento de manera más eficiente, evitando tiempos de inactividad prolongados.
2. Reducción de costos: La integración de equipos y sistemas permite una mejor gestión de los recursos, lo que se traduce en una reducción de costos. Por ejemplo, al utilizar herramientas de gestión de activos, es posible llevar un control más preciso de los repuestos y evitar compras innecesarias. Además, al optimizar la planificación y programación, se pueden reducir los gastos asociados a tiempos de inactividad y reparaciones de emergencia.
3. Mayor eficiencia en la ejecución de tareas: Al integrar los equipos de mantenimiento con sistemas de gestión de mantenimiento asistido por computadora (CMMS), se facilita la asignación de tareas, el seguimiento de su ejecución y la recopilación de datos para su análisis. Esto permite una mayor eficiencia en la realización de las tareas de mantenimiento, reduciendo los tiempos de respuesta y mejorando la calidad del trabajo realizado.
Estrategias para integrar equipos y sistemas
Para lograr una integración efectiva de los equipos y sistemas en la gestión del mantenimiento, es importante seguir algunas estrategias clave:
- Establecer canales de comunicación claros y fluidos entre los diferentes departamentos y equipos involucrados en el mantenimiento.
- Implementar un sistema de gestión de activos que permita un control más preciso de los repuestos y equipos.
- Utilizar un CMMS que facilite la asignación de tareas, el seguimiento de su ejecución y la generación de informes.
- Realizar reuniones periódicas para evaluar el desempeño del equipo de mantenimiento y hacer ajustes en la planificación si es necesario.
La integración de equipos y sistemas es fundamental para optimizar la gestión del mantenimiento. Al establecer una comunicación fluida y utilizar herramientas tecnológicas adecuadas, es posible mejorar la planificación y programación, reducir costos y aumentar la eficiencia en la ejecución de tareas de mantenimiento.
Mejorar la planificación y programación de las tareas de mantenimiento
Una forma efectiva de optimizar la gestión del mantenimiento es mejorar la planificación y programación de las tareas. Esto implica establecer un calendario detallado de las actividades de mantenimiento que deben realizarse, teniendo en cuenta la frecuencia y la prioridad de cada una.
Además, es importante asignar los recursos necesarios para cada tarea, como personal, herramientas y materiales. De esta manera, se evitan retrasos y se maximiza la eficiencia en la ejecución de las labores de mantenimiento.
Asimismo, es recomendable utilizar herramientas de software especializadas en la gestión del mantenimiento, las cuales permiten llevar un registro de las actividades realizadas, los recursos utilizados y los resultados obtenidos. Estas herramientas facilitan la programación de las tareas, la asignación de recursos y el seguimiento de los trabajos en curso.
Optimizar el uso de los recursos humanos
El personal de mantenimiento es uno de los recursos más importantes en la gestión del mantenimiento. Por ello, es fundamental optimizar su utilización y aprovechar al máximo sus habilidades y conocimientos.
Una forma de lograrlo es asignar las tareas de acuerdo a las habilidades y especialidades de cada trabajador. De esta manera, se garantiza que cada tarea sea realizada por la persona más adecuada para ello, lo que aumenta la eficiencia y reduce la posibilidad de errores.
También es recomendable llevar a cabo una adecuada planificación de la carga de trabajo, evitando asignar más tareas de las que el personal puede realizar en un determinado período de tiempo. Esto evita el estrés y la saturación de los trabajadores, lo que a su vez reduce la posibilidad de errores y accidentes laborales.
Optimizar el uso de los recursos materiales
Además de los recursos humanos, los recursos materiales también juegan un papel fundamental en la gestión del mantenimiento. Es importante optimizar su uso y asegurarse de contar con las herramientas y materiales necesarios para llevar a cabo las tareas de mantenimiento de manera eficiente.
Para lograrlo, es recomendable llevar un inventario actualizado de los recursos materiales disponibles, incluyendo herramientas, repuestos y materiales consumibles. Esto permite conocer en todo momento qué recursos están disponibles y cuáles necesitan ser adquiridos o reemplazados.
Además, es importante establecer un sistema de control y seguimiento de los recursos materiales utilizados en cada tarea de mantenimiento. De esta manera, se evita el desperdicio y se optimiza su uso, reduciendo los costos asociados al mantenimiento.
Realizar un mantenimiento correctivo eficiente para minimizar paradas no planificadas
El mantenimiento correctivo es una tarea esencial en la gestión de activos y la optimización de recursos. Sin embargo, es importante realizar este tipo de mantenimiento de manera eficiente para minimizar las paradas no planificadas y maximizar la disponibilidad de los equipos.
Para lograr esto, es necesario seguir algunos pasos clave:
1. Identificar las causas raíz de las averías
Antes de llevar a cabo cualquier reparación, es fundamental identificar las causas raíz de las averías. Esto implica analizar detalladamente los registros de mantenimiento, realizar pruebas y evaluar el rendimiento del equipo. Al determinar la causa raíz, se podrán implementar soluciones más efectivas y duraderas.
2. Priorizar las reparaciones
No todas las averías tienen el mismo impacto en la operación. Es importante priorizar las reparaciones en base a su criticidad y el impacto que puedan tener en la producción. De esta manera, se podrán asignar los recursos adecuados y dar respuesta a las averías de manera más eficiente.
3. Contar con un stock de repuestos adecuado
Uno de los principales obstáculos para realizar un mantenimiento correctivo eficiente es la falta de repuestos. Es fundamental contar con un stock de repuestos adecuado y gestionarlo de manera eficiente. Esto implica llevar un control exhaustivo de los repuestos utilizados, realizar un seguimiento de los niveles de inventario y tener acuerdos con proveedores para garantizar una pronta entrega de repuestos.
4. Establecer un plan de mantenimiento preventivo
Si bien el mantenimiento correctivo es esencial, la mejor manera de minimizar las paradas no planificadas es a través de un mantenimiento preventivo adecuado. Establecer un plan de mantenimiento preventivo permite identificar y corregir problemas potenciales antes de que se conviertan en averías mayores. Esto ayuda a reducir la necesidad de mantenimiento correctivo y optimiza la disponibilidad de los equipos.
5. Capacitar al personal de mantenimiento
El personal de mantenimiento juega un papel crucial en la eficiencia del mantenimiento correctivo. Es importante capacitar a los técnicos en las mejores prácticas de mantenimiento, en el uso de herramientas y en la identificación de problemas. Al contar con un personal capacitado, se podrá llevar a cabo el mantenimiento de manera más eficiente y reducir el tiempo de respuesta ante averías.
Realizar un mantenimiento correctivo eficiente es fundamental para minimizar las paradas no planificadas y optimizar la disponibilidad de los equipos. Siguiendo los pasos mencionados anteriormente, se podrá gestionar de manera más eficiente el mantenimiento correctivo y optimizar los recursos disponibles.
Realizar un análisis de costos para identificar oportunidades de ahorro
Para optimizar los recursos en la gestión del mantenimiento, es fundamental realizar un análisis de costos detallado. Este análisis nos permitirá identificar oportunidades de ahorro y tomar decisiones informadas para mejorar la eficiencia en el uso de los recursos.
El primer paso para realizar este análisis es recopilar información sobre los costos asociados con el mantenimiento. Esto incluye no solo los costos directos de los materiales y la mano de obra, sino también los costos indirectos, como el tiempo de inactividad de los equipos y los costos de energía.
Una vez que tengamos esta información, podemos utilizar diferentes técnicas de análisis, como el **análisis ABC**, para identificar los elementos de mayor impacto en los costos totales. Esto nos ayudará a priorizar nuestras acciones de optimización y enfocar nuestros esfuerzos en los aspectos más críticos.
Además, es importante tener en cuenta que no todos los costos son iguales. Algunos costos, como los de **mantenimiento preventivo**, pueden ser vistos como una inversión a largo plazo para evitar fallas costosas. Por lo tanto, es necesario evaluar cuidadosamente los beneficios y los costos asociados con cada actividad de mantenimiento.
Otra herramienta útil para identificar oportunidades de ahorro es el **benchmarking**. Comparar nuestros costos y prácticas con los de otras empresas en la industria nos permitirá identificar áreas en las que podemos mejorar y adoptar mejores prácticas.
Realizar un análisis de costos detallado nos ayudará a identificar oportunidades de ahorro y mejorar la eficiencia en la gestión del mantenimiento. Recopilar información sobre los costos, utilizar técnicas de análisis y realizar benchmarking son algunas de las estrategias que podemos utilizar para lograr estos objetivos.
Promover la cultura de la eficiencia en la gestión del mantenimiento
La optimización de recursos en la gestión del mantenimiento es una práctica fundamental para garantizar el buen funcionamiento de cualquier empresa o industria. Para lograrlo, es necesario promover una cultura de eficiencia que permita el uso adecuado de los recursos disponibles.
En este sentido, es importante establecer una planificación estratégica que permita identificar las necesidades de mantenimiento y definir las acciones que se deben llevar a cabo para garantizar su correcta ejecución. Esto incluye la elaboración de un plan de mantenimiento preventivo, que permita realizar las labores necesarias de manera programada y evitar así la aparición de averías o paradas no planificadas.
Además, es fundamental contar con un equipo de trabajo capacitado y comprometido, que cuente con los conocimientos y habilidades necesarias para llevar a cabo las tareas de mantenimiento de manera eficiente. Esto implica brindar la formación y el entrenamiento adecuados, así como proporcionar las herramientas y los recursos necesarios para desempeñar su labor de manera óptima.
Asimismo, es importante fomentar la comunicación y la colaboración entre los diferentes departamentos de la empresa, especialmente entre el departamento de mantenimiento y el de producción. Esto permitirá anticiparse a posibles problemas o necesidades, así como optimizar los recursos disponibles para llevar a cabo las tareas de mantenimiento de manera eficiente.
Por otro lado, es fundamental establecer un sistema de gestión de inventario y de control de repuestos, que permita tener un registro actualizado de los materiales y piezas disponibles, así como de su ubicación y estado. Esto facilitará la planificación y ejecución de las labores de mantenimiento, evitando retrasos o paradas innecesarias debido a la falta de repuestos.
La optimización de recursos en la gestión del mantenimiento es esencial para garantizar el buen funcionamiento de una empresa o industria. Para lograrlo, es necesario promover una cultura de eficiencia que incluya una planificación estratégica, un equipo de trabajo capacitado, una comunicación fluida entre los departamentos y un adecuado sistema de gestión de inventario y control de repuestos.
Preguntas frecuentes
1. ¿Qué es la optimización de recursos en la gestión del mantenimiento?
La optimización de recursos en la gestión del mantenimiento es el proceso de utilizar de manera eficiente los recursos disponibles para mantener en buen estado los activos de una organización.
2. ¿Cuáles son los beneficios de optimizar los recursos en la gestión del mantenimiento?
Al optimizar los recursos en la gestión del mantenimiento se pueden reducir los costos, mejorar la eficiencia operativa y prolongar la vida útil de los activos.
3. ¿Qué estrategias se pueden utilizar para optimizar los recursos en la gestión del mantenimiento?
Algunas estrategias que se pueden utilizar incluyen la planificación y programación eficiente de las tareas de mantenimiento, la implementación de un sistema de gestión de activos y la utilización de tecnologías de monitoreo y diagnóstico.
4. ¿Cómo se puede medir la eficiencia en la gestión del mantenimiento?
La eficiencia en la gestión del mantenimiento se puede medir a través de indicadores clave de rendimiento como el tiempo medio entre fallas, el tiempo medio de reparación y el costo de mantenimiento por unidad de producción.
Deja una respuesta
Tal vez te puede interesar: